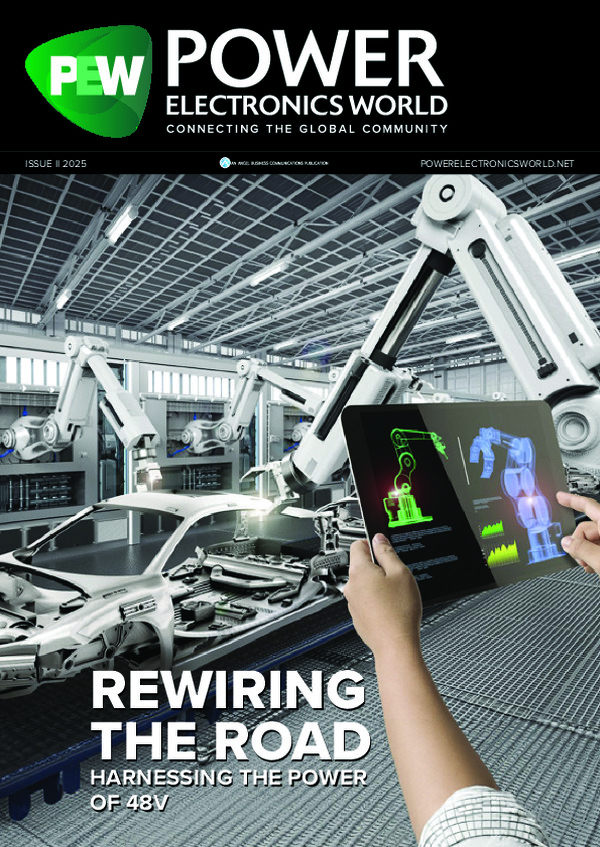
Rewiring the road PART 2
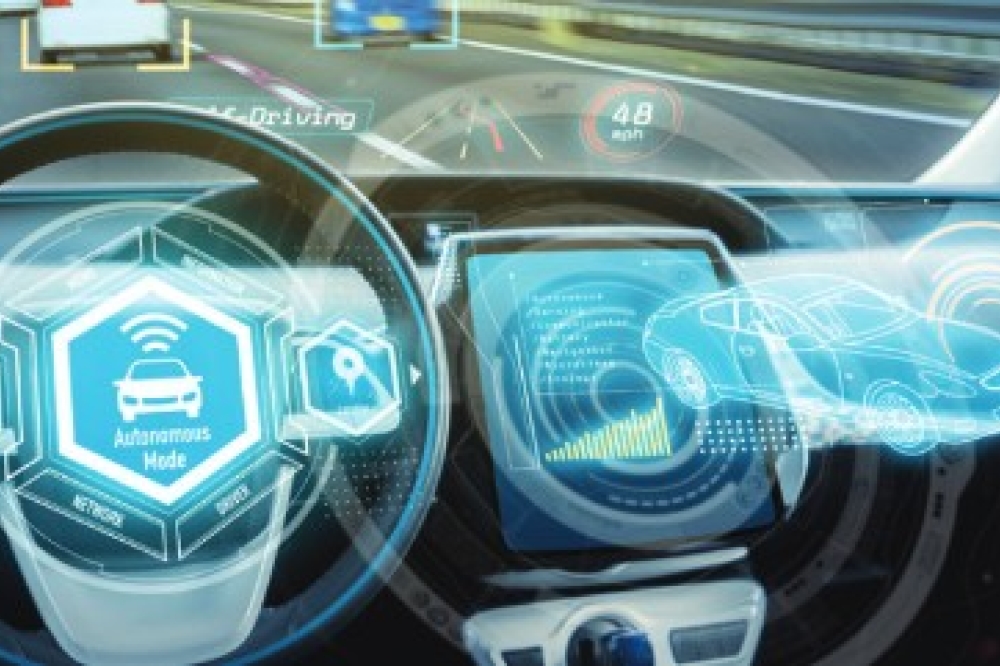
Harnessing the power of 48V. Part 2.
By Kirk Ulery, Business Development Manager, Molex Transportation Solutions.
As the modern driving experience demands more electronics, the shift toward 48V electrical system technology is rapidly gaining traction, disrupting traditional automotive power architectures. Today’s increasingly electrified vehicles need more. This surge in demand is propelling innovation and investment in 48V systems as automakers seek to enhance vehicle performance and efficiency.
Are we at a tipping point?
48V technology is a key enabler for advanced automotive features such as electric turbocharging, regenerative braking and advanced infotainment systems. It provides a compelling solution for a range of vehicles, from gas-powered to electric,
and is poised for widespread adoption.
But it’s not that easy. For 48V systems to be successfully implemented, challenges such as standardization and cost reduction must be addressed.
How do we clear the hurdles to move forward? What will it take for 48V power to become the new normal? Let’s explore these questions together.
Potential of 48V in emerging vehicle segments
The development of 48V power systems provides additional opportunities beyond passenger car in-vehicle features and accessories. It extends to promising potential gains in emerging vehicle segments. Off-road vehicles can leverage 48V power to tackle challenging terrain. Electric power assist for steering, suspension and winches can elevate off-road performance and capability. Additionally, 48V systems can bolster vehicle stability and control in demanding conditions.
Electric and hybrid powertrains benefit from 48V technology as a foundational step toward full electrification. By supplementing electric motors and components, 48V systems optimize performance and efficiency in hybrid vehicles. Also, 48V supports functions like battery management and thermal management, ensuring optimal system operation.
Specialized vehicles, such as those used in agriculture, construction and mining, can harness 48V power to increase productivity and efficiency. By powering hydraulic pumps, compressors and other auxiliary systems electrically, these vehicles can achieve improved performance, reduced operator fatigue and greater responsiveness. This shift to electric-powered components aligns with industry trends toward more efficient, reliable systems, like the development of electric steering and braking in automobiles.
Autonomous vehicles (AVs) rely on robust power systems, and 48V technology delivers. By supplying reliable power to sensors, actuators and control units, 48V facilitates the advanced functionality needed for autonomous driving. Although full autonomous vehicle deployment is still in its early stages, 48V will certainly help AVs along their path toward more widespread deployment. By targeting these emerging vehicle segments, the 48V technology can expand its market reach and contribute to the overall electrification of the transportation industry.
The journey to full 48V adoption a strategic, phased approach for the successful transition from 12V to 48V
The automotive industry is undergoing a major transformation as it moves from traditional 12V electrical systems toward more advanced electrified powertrains. While fully electric vehicles are gaining traction in market share, mild hybrid electric vehicles (MHEVs) with 48V systems offer a viable interim solution. These vehicles combine the benefits of electrification with the familiarity of internal combustion engines. MHEVs deliver these advantages without the significant costs and infrastructure requirements associated with EVs.
Despite the promise of 48V technology, its adoption is still in the relatively early stages. While some automakers have introduced mild hybrid models, the technology is far from reaching its full potential. To accelerate the transition to a 48V future, a comprehensive roadmap is essential. The following guide outlines key strategies to answer the question: how do we get from here to there?
Develop modular 48V platforms
A modular 48V platform offers a standardized, flexible architecture that can be tailored to various vehicle sizes, types and power demands. This platform consists of interchangeable components, such as electric motors, inverters, DC-DC converters and batteries, which can be combined in different configurations to meet specific vehicle needs.
Like building blocks, this approach enables automakers to efficiently develop and produce a diverse range of vehicles while maximizing component sharing and reducing development costs. Ideally, a modular 48V platform would be utilized across a broad spectrum of vehicles within an automaker’s lineup.
By developing modular 48V platforms, automakers can elevate economies of scale, shorten time to market and maintain the flexibility to adapt to changing market trends and consumer preferences. This standardized approach also simplifies the integration of advanced features, such as electric power steering, electric compressors and thermal management systems.
Foster collaboration
Strategic partnerships are key to accelerating 48V system development and expanding market penetration. Automakers and component suppliers must collaborate to overcome technical challenges and establish industry standards. This close cooperation is essential for optimizing system integration, reducing development costs and speeding up time to market.
Joint research and development should focus on upgrading components such as inverters, electric motors and energy storage systems. Equally important is establishing standardized communication and electrical architectures to ensure smooth integration across different vehicle models. By pooling expertise and resources, the industry can work together to broaden the market reach of 48V systems.
Continued technological advancements
Ongoing research and development are crucial to fine-tuning 48V system performance and reducing costs over time. And these are key to accelerating widespread adoption. Focus areas include advancing battery technology to increase energy density, power output and lifespan while finding cost-saving opportunities.
Automotive design engineers must also prioritize the development of more efficient and compact power electronics, such as inverters and DC-DC converters, to improve system capabilities and minimize losses. Advancements in electric motors and generators, particularly in power density and torque output, are also important for fine-tuning system performance.
Additionally, innovative thermal management solutions are vital to maintaining optimal operating conditions for 48V components and extending their lifespan.
By following these steps and applying knowledge gained along the way, the automotive industry can gradually transition to full 48V adoption while mitigating risks and maximizing benefits.
The role of zonal architecture in facilitating 48V integration
Zonal architecture provides a clear advantage over traditional vehicle electrical systems when incorporating 48V technology. By segmenting the vehicle into distinct electrical zones, each with its own control unit and power supply, this approach simplifies the implementation of 48V components.
Enhanced Flexibility and Scalability
Encouraging greater design flexibility for 48V systems, zonal architecture permits automakers to customize voltage levels and component selection for each zone, maximizing performance and efficiency. Additionally, this architecture supports easier scalability across various vehicle models, accelerating time-to-market.
Better power distribution
Managing power distribution within specific zones reduces electrical losses and boosts system efficiency. With dedicated power supplies for each zone, voltage levels are fine-tuned for different components, bolstering overall vehicle
performance.
Reduced wiring complexity
Zonal architecture simplifies the vehicle’s electrical wiring, reducing weight, cost and manufacturing complexity. Fewer wires and connections also mean a lower risk of electrical faults.
Superior system reliability
By distributing control and incorporating multiple power supply points, zonal architecture improves redundancy and fault tolerance. In the event of a failure in one zone, the system can continue operating with minimal disruption.
As the automotive industry transitions to electrified powertrains, zonal architecture will be vital to optimizing vehicle performance and reducing development costs.
Small and scrappy or tried-and-true? A balanced mindset for accelerating 48V deployment
Established automakers, known for their engineering prowess and manufacturing capabilities, have long driven automotive innovation. However, with rapid technological advancements and shifting consumer preferences, a more agile approach is essential. Startups innovate quickly and adapt to market changes, while traditional automakers offer resources and decades of experience. By merging these strengths, the industry can accelerate the integration of transformative technologies like 48V systems.
Key strategies for nimble progress
Traditional automotive manufacturing processes optimized for large-scale production can present challenges for rapid 48V system development. To overcome these hurdles, automakers must adopt agile methodologies tailored to the unique characteristics of 48V technology.
Integrating practices such as rapid prototyping, iterative design, and flexible manufacturing can significantly accelerate product development and enhance overall efficiency.
Cross-functional teams and flexible project management
Automakers can benefit from expanding efforts to speed up 48V deployment through cross-functional teams. By bringing together diverse expertise from engineering, design, marketing and other areas, these teams create a collaborative environment that mirrors the agile structure of startups, enabling traditional automakers to respond more effectively to customer desires.
Agile methodologies, initially rooted in software development, are now being embraced by automakers. Frameworks like Scrum and Kanban empower teams to work flexibly, prioritize tasks effectively, and deliver results efficiently.
Iterative development
Automakers should adopt an iterative development model to shorten development timelines and enhance responsiveness. This approach allows teams to rapidly prototype, test and refine 48V systems by breaking the process into smaller, manageable cycles. It’s a calculated approach that minimizes risks by focusing on incremental improvements rather than overhauling entire systems.
A customer-centric approach
Prioritizing customer feedback ensures that product development aligns with consumer needs. Companies that excel in this area build strong customer relationships, delivering features and experiences that address pain points and resonate with drivers. Engaged customers often become brand advocates, encouraging adoption, positive perceptions and sales.
Partnerships and collaborations
Strategic partnerships with tech startups, component suppliers and research institutions enable automakers to leverage cutting-edge advancements in automotive technology. Collaborations focused on specific 48V components, systems integration or battery technology can yield groundbreaking results and bring new products to market faster.
Differentiated benefits
Applying startup strategies to established automakers’ processes can unlock a unique set of advantages. By combining the best of both worlds –proven techniques and startup speed – automakers can set themselves apart from the rest of the field.
Accelerated market response
Automakers can cultivate a culture of rapid decision-making and iteration by empowering smaller, cross-functional teams. This nimble approach supports faster development cycles, quicker market entry and the ability to swiftly adapt to evolving trends and consumer preferences, providing a competitive edge.
Increased product innovation and enhanced product quality
Dedicated teams focused on specific 48V projects encourage experimentation and rapid problem solving. This facilitates swift prototyping and testing, potentially leading to advanced solutions that address quality issues, augment reliability and ultimately deliver superior product performance.
By integrating quality assurance into this agile framework, automakers can balance speed and innovation with proven reliability, ensuring new 48V systems meet stringent standards. Leveraging testing protocols, automakers lower risks associated with rapid development. Combining rigorous testing with agile practices, they identify and address potential issues early, differentiating them from newer companies and traditional competition.
Implementing these strategies significantly boosts automakers’ ability to innovate, adapt and compete in the rapidly evolving automotive market.
Molex: driving automotive advancements with every connection
As a global leader in connectivity solutions, Molex is driving support for the development of vehicles with 48V systems. The MX150 Mid-Voltage Connector system exemplifies our commitment to addressing the evolving needs of the automotive industry.
Engineered for efficient assembly and reduced package size, the MX150 delivers a robust, reliable solution for 48V wiring applications. Capable of handling up to 60V, this connector system supports using smaller wire gauges to reduce both weight and cost while maintaining high performance. Its versatility and compatibility with oil-cooled electric motors make the MX150 a top choice for automotive manufacturers.
Molex is committed to forging strong customer partnerships and developing tailored solutions that tackle industry challenges. By combining our technical expertise with customer insights and powerful automotive design and manufacturing capabilities, we are shaping the future of automotive connectivity in a 48V world.