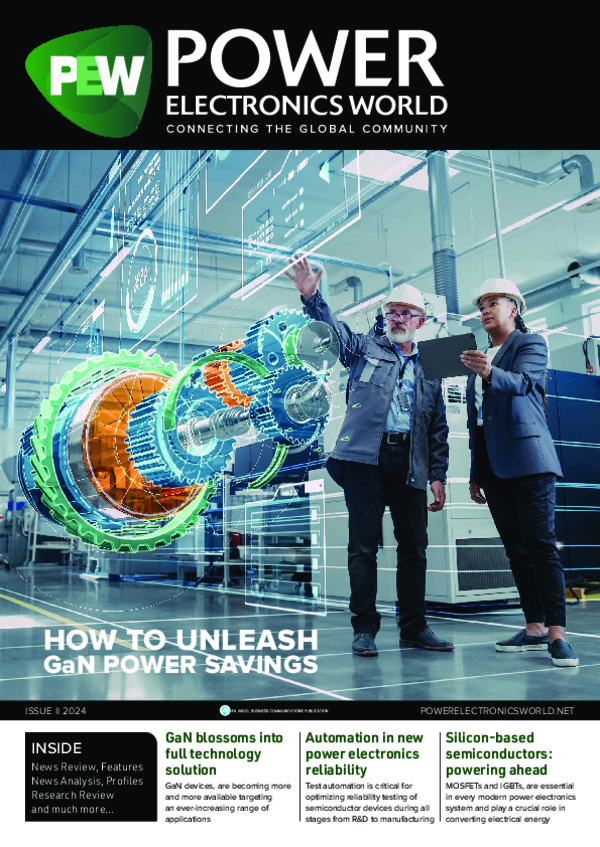
How to unleash the power savings of GaN
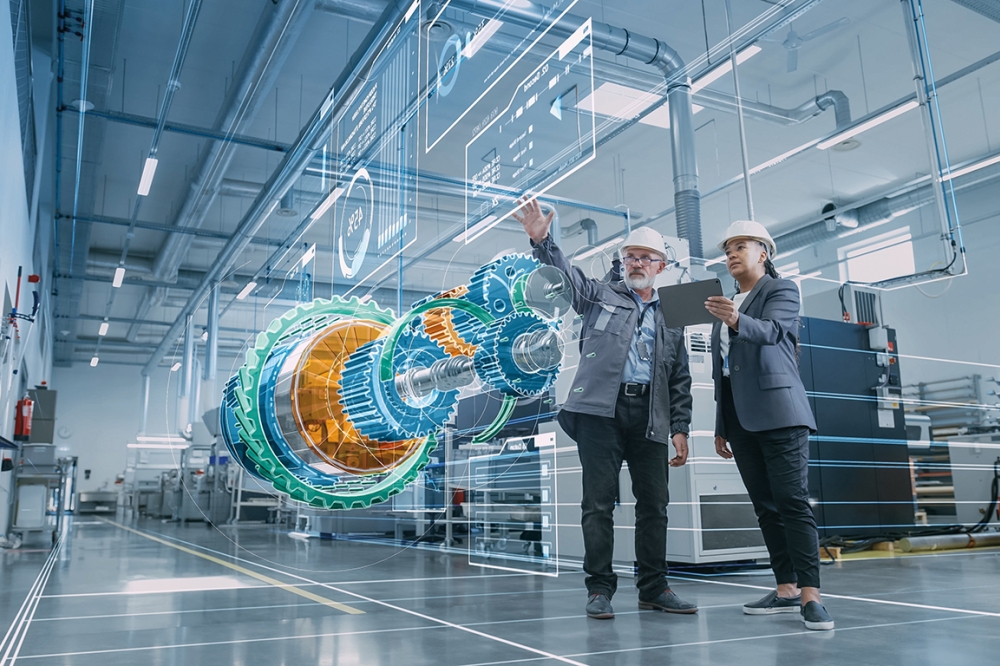
Everyone wants to do something about climate change and we have a solution that could have a major impact on reducing CO2 production. Sometimes, with our tongue firmly in our cheek, we say “saving the planet through better motor drives”.
Electric motors currently use 50% of global electricity, most of which is produced from burning fossil fuels. This will increase due to the inevitable move to electrification to hit net zero targets with rapidly increasing numbers of heat pumps and electric vehicles
Electric motors and systems are the largest, single-energy, end use and account for half of global electricity consumption according to a recent International Energy Agency report. This report expects that, without policy change by 2030, electromagnetic motor use will produce 8,570 Gigatonnes of CO2 per year.
The elephant in the room is the fact that electric motors are often shockingly inefficient. Depending on the application, up to 25% of the electricity is wasted. Reducing this wastage means less CO2 has to be produced. The International Energy Agency said “There is a huge, untapped potential for energy efficiency in electric motors. However, the energy efficiency of motors has been neglected in comparison with other sustainable energy opportunities.”
77% of electric motors do not use motor control electronics (variously called controller, inverter or Variable Frequency Drive - VFD) to control them which is very inefficient. The remaining 23% have VFDs to adjust the motor speed which is less wasteful. However, these are still inefficient. This is because they use slow transistors as switches. The faster the transistors in the VFD switch, the less time is spent in the transition zone where energy is wasted: VFDs today often switch at only 4kHz.
Traditionally silicon (Si) transistors have been used but
they are reaching the limits that they can be switched at so faster Silicon
Carbide (SiC) transistors are being used. For example, in the automotive world,
SiC is now increasingly used in traction inverters. However, trying to drive
either technology even faster, with frequencies higher than 100kHz to reduce
wastage, creates problems with overheating and RF interference (RFI).
GaN is inherently a better semiconductor than Si or SiC. It has less capacitance, faster switching and no body diode. But it has been hard to use and has a reputation for being fragile.
The graph shows that GaN has the ability to switch much faster than SiC - but it also shows how people must think GaN can only be used at low power (up to 10kW). This is what QPT solves with its qGaN technology.
At present, GaN has had to be confined to the low power applications and soft switching that uses less that 100kHz, such as chargers and computer power supply units with a TAM of $15bn. This new approach unleashes GaN to be driven at high speed to live up to its full potential and thus unlocking a huge new market of high-power, high-performance applications in HVAC, industrial application and electric vehicles with a TAM of $60bn.
The problem is that when you go above this 100 kHz point, you are in RF microwave territory. Power Electronics is currently about high power in the kWs with tens to hundreds of Amps but only low frequencies in the KHz. Microwave is typically low power in the mWs and high frequencies in the MHz. QPT’s solution is to deploy microwave techniques so that these two problems of overheating and RF interference are solved. Combining them together opens up a new future for Power Electronics kW and MHz, i.e., tens to hundreds of Amps at MHz speeds and dramatically higher efficiencies.
As a result, GaN transistors can be driven many times faster than any existing technology.
This has two implications. The first is dramatically less
time in the transition region where energy is wasted. The diagram shows that
the rise and fall times (Tr & Tf) where energy is wasted in the resistive
region) are less than one nanosecond.
The illustration on the left shows the sloping rise and fall where there switching losses whilst below these are near straight up
and down so switching losses are dramatically reduced. Secondly, because the
transistors are switching faster (< 1ns Tr/Tf), we can use a higher
frequency Pulse Width Modulation (PWM) signal. Instead of 4kHz or 100KHz, the
QPT system typically runs at 1MHz and could be even faster.
This enables a sinus filter to be integrated into the architecture because the frequency is high so smaller, cheaper filters can be used to reduce size, cost and weight.
Also, because the PWM frequency is so far from the motor drive frequency, the Low Pass Filter (LPF) action is very effective. Whereas most VFDs send a “dirty” PWM to the motor, the QPT output is almost pure sine, which very much better for the motor with less eddy currents (which cause heat & stress on the windings), less acoustic noise & vibration, essentially no dV/dt stress, no DC path, lower torque ripple, etc.
This means that a VFD can now be created that is up to 80% more efficient. In overall terms of total electricity usage by the VFD and motor together, this equates to a reduction of around 10% depending on the application. Plus, with less waste heat and stresses, the motor reliability improves to give a longer MTBF.
So, what could this disruptive technology breakthrough deliver when deployed? We calculate that the improved efficiency equates to a potential of $66bn in annual energy savings, a saving of 1000TWh and even more importantly 400m tonnes of CO2 that does not have to be produced.
Our qGaN module
Because our solution combines two different disciplines,
we have created a module that has all our qGaN technologies incorporated
together heat sink and RF shielding.
QPT’s qGaN modules are designed with RF considerations in mind. The packaging and construction of the module allow for switching at the order of MHz without issues with EMC (electromagnetic compatibility). This technology is currently capable of producing 7.5kW motor drives, which are vital in the industrial sector for things such as conveyor belts, mixers, and air conditioning.
QPT has a roadmap for high-power drives, ranging from 20 to 120kW, and anticipates these to launch over the next year. Furthermore, with much less wasted energy, the module wastes less heat, eliminating the need for an active cooling system or heavy heatsink, or at least reducing the requirements of such systems. By adding copper around the die to conduct thermal energy away, there will be parasitic capacitance couplings, which degrade the switching characteristics of the transistor. QPT’s passive cooling solution conducts heat away without the need for this.
Our VFD demonstrator
We have created a VFD that is a drop-in replacement for a
common VFD to make it easy for manufacturers to include into their motor
designs and even retro fit to existing ones so that they can take rapidly
implement of its ultra-efficient and ultra-compact design. The elimination of
RF interference means that costly, bulky cables to connect the VFD to the motor
are eliminated. In fact, the VFD is now so small at a twentieth of the size of
current equivalents that it can be mounted on the motor to create a compact,
integrated solution.
This is a 400V (230V 3 phase), 7.5kW qGaN VFD. It has a 1MHz internal switching PWM with less than 1 ns switching time and a compact integrated sinus filter. The output is from zero to 500Hz (0-300rpm) with pure wave (~0% THD). The active rectifier has less than 5% THD, no electrolytic capacitors and therefore a high MTBF.
Summary
The current thinking is
that SiC is the next great thing for Power Electronics with huge investments to
support it. But, while SiC has its place, GaN is fundamentally a better
semiconductor and will displace Si and SiC in many applications with motors being
one.
As we have shown, there is a barrier of overheating and RFI for SiC that is becoming increasingly apparent when trying to use it for more challenging applications and is being ignored in all the SiC hype. Our GaN technology enables GaN to greatly surpass SiC with much greater efficiencies and power handling capabilities so that it will be the true future of Power Electronics.
Saving the planet through GaN may seem be a hyperbole but
net zero and the electrification of everything are critical for humanity and we
need to be doing everything we can to get there.
Those of us in the PE community have the challenge to make this work: but it is a challenge we need to rise to for the sake of our planet and our children. Better technologies like GaN at these higher frequencies to reduce energy wastage can have a big part in making this happen.