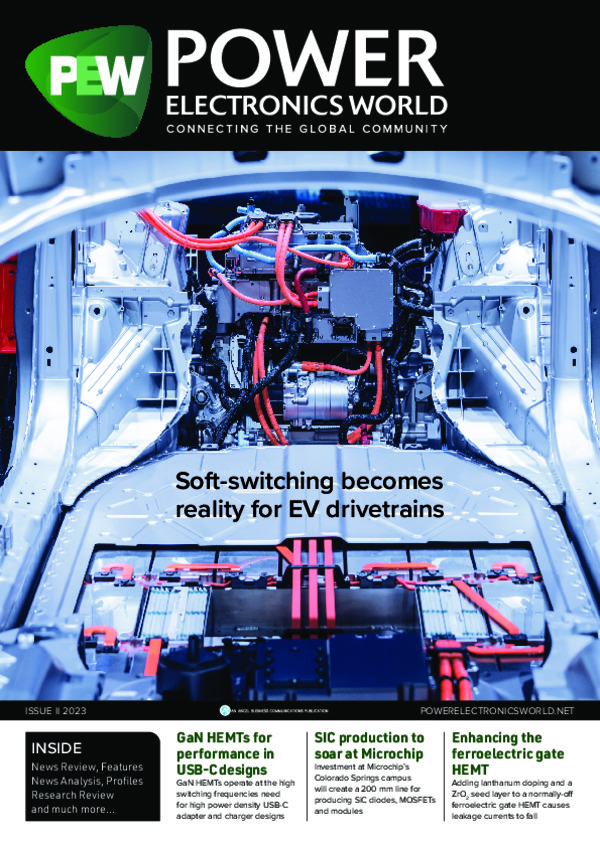
Driving motors in space
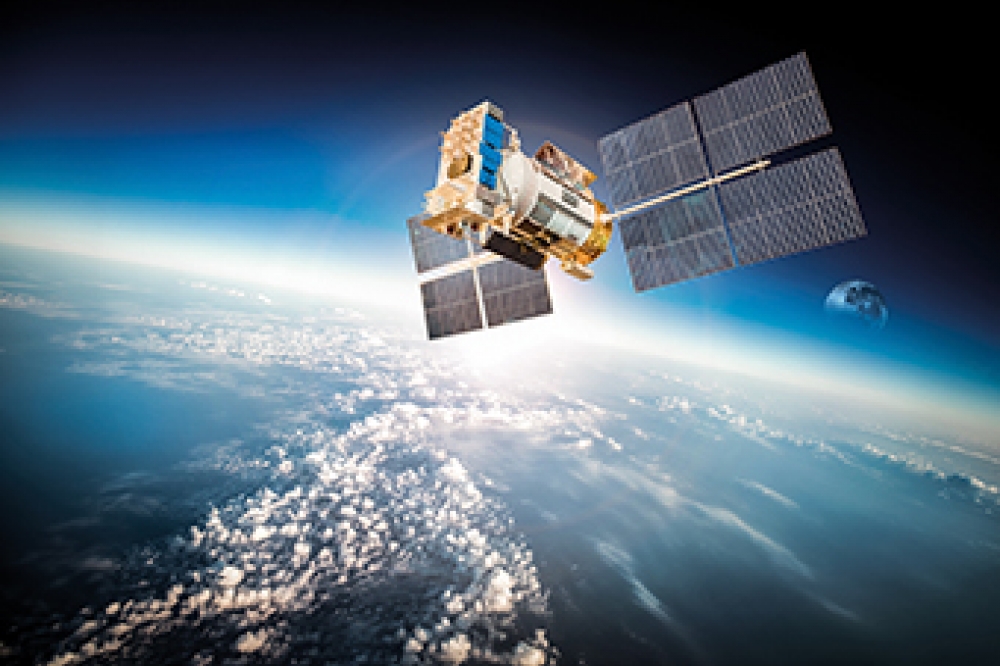
Its intrinsic radiation hardness and excellent electrical
characteristics position the GaN HEMT as the ideal device for making
circuits that drive motors in space.
BY ANTHONY MARINI AND MAX ZAFRANI FROM EPC SPACE
The number of satellites circling the globe in a low-Earth orbit is increasing at an astonishing rate. Back in 2019, active and defunct satellites totalled just over 3,000; today it’s around 10,000; and by the end of this decade this figure will have rocketed to several hundred thousand.
This breath-taking growth in the level of activity in the outer reaches of the Earth’s atmosphere has ensured that ventures and activities that at one time appeared far-fetched are now a certainty. That includes the commercial development of this sector, which is well underway, as well as manufacturing in space.
The latter, an activity that offers intriguing possibilities, will involve the use of all types of motors to perform every mundane and precision task associated with manufacturing. For those designing manufacturing systems for space, as well as having to source the most appropriate motor, efforts will need to be directed at carefully selecting the most appropriate driver, to ensure that the motor runs efficiently and reliably. Making such decisions are not easy, because the motor and its driver behave as a tandem entity, with their interplay determining the system’s mechanical and electrical attributes – both criteria are of critical importance for overall system performance. Partner a motor with an inferior driver and it will be incapable of operating efficiently and delivering its peak performance. Note that up in space efficiency really matters, alongside radiation hardness – excellence on both these fronts is needed without compromising the mechanical attributes of the motor, such as its speed and positional accuracy.
Figure 1. A single-phase motor driver with speed and direction control.
Figure 2. Depletion-mode (top) and enhancement-mode (bottom) GaN transistor structures.
Varying requirements
When using a motor in space, there are specific challenges that depend on the physical location of the system, particularly with regards to radiation. Satellites orbiting the Earth have to handle radiation fields that are not found in stationary locations, such as the surface of the Moon or Mars.
Two classes of radiation are found in space: cosmic radiation, coming from high-energy particles that are moving at relativistic speeds; and lower energy protons and electrons from the solar wind, trapped in Van Allen radiation belts, due to the Earth’s magnetic field.
When sensitive electronics is deployed in space, it is surrounded by shielding. However, there is a limit on how much shielding can be applied. Shielding adds mass to the launch – this incurs substantial costs, due to the energy required to either place objects in orbit or to escape the Earth’s gravity. This cost-related limitation is particularly pressing in commercial space ventures, where financial margins really matter, and where constellations of low-cost satellites are stationed in primarily low-Earth orbits.
Figure 3. (a) Gate-to-source forward leakage, IGSSF vs. total dose.
(b) Gate-to-source reverse leakage ,IGSSR vs. total dose. (c)
Drain-to-source leakage IDSS vs. total dose. (d) On-resistance, RDS(ON)
vs. total dose. (e) Gate-source threshold voltage, VGS(th) vs. total
dose.
Due to this state-of-affairs, there’s a need for electronics that has an inherent radiation ‘hardness’ or tolerance, and can survive high-energy insults and longer-term, lower-dose radiation exposure over the duration of the planned mission.
Another factor influencing the type of radiation, and its magnitude, that electronics will encounter in Earth’s orbit is the altitude of the satellite. The radiation hardness requirement for a satellite in a low-Earth-orbit differs from that in a geosynchronous Earth orbit – and both these sets of requirements differ from those for landers and missions to the Moon and other planets, and for deep space probes. In all cases, those working on their particular ventures must consider the radiation profile over the life of the satellite or spacecraft, and carefully select every component within the motion control system to prevent its premature failure.
For motion control systems under bombardment by radiation, their weakest link is the electronics associated with their motor drives. The motors themselves are not a concern, as they provide a very robust component of the system – they are constructed from wire, and thus present an inherent radiation hardness during operation. That’s not the case for the electronics that comprise the motor driver. This driver contains numerous interconnected semiconductor components, including: power switches for motor windings; associated catch diodes; and electronics that interfaces between circuity. All circuits and constituent components have to have an assured/tested level of radiation hardness to ensure that the mission will succeed long-term.
Figure 4. (a) Gate-to-source leakage, IGSS vs. neutron fluence. (b)
Drain-to-source leakage, IDSS vs. neutron fluence. (c) Gate-source
threshold voltage, VGS(th) vs. neutron fluence. (d) (d) On resistance,
RDS(ON) vs. neutron fluence.
There are operational implications from a radiation-induced event, ranging from erratic operation to outright system failure. Consider the case where a motor phase is being driven in an H-bridge configuration, as shown in Figure 1. In this circuit, the switches S1 through S4 represent the power switch transistors driven by the gate drivers. As depicted in Figure 1 (a), for the forward motor direction switches S1 and S4 are closed/switched; and for the reverse direction, switches S2 and S3 are closed/switched. In both cases, it is the pulse-width modulation control of the switches that determines the speed of the motor.
If high-energy radiation disrupts the gate driver circuit or the output power switch, represented by S1-S4, this can cause S1 to S4 to either open or close momentarily. In the open switch case no damage occurs, and the only downside is a missed switching opportunity. But in the closed case, the damage can be catastrophic. For example, consider what could happen when S4 is induced closed by radiation when it isn’t supposed to be, and S3 is simultaneously closed in normal reverse-direction operation. In that scenario, shown in Figure 1 (b), a cross-conduction event will occur from VDD-to-ground through S3 and S4, destroying one or both switches. Clearly, this event, arising from uncontrolled current flow, must be avoided at all costs.
In the space environment, GaN transistors are ideal candidates for rad-hard transistor switches. These devices are blessed with an inherent tolerance to total ionizing dose radiation. They can be exposed to megarads of radiation without serious consequence; the only noteworthy changes are a slight rise in the gate and drain leakage currents. Thanks to their lateral structure and the absence of gate oxides and substrate-related junctions, these devices are immune to damage from interaction with single, energetic particles, so long as the transistor is well designed (see Figure 2). The robustness that a 200 V, 18 A discrete GaN HEMT provides is illustrated by typical radiation performance data. This device is adept at handling ionising doses (see Figure 3), neutron radiation (see Figure 4) and heavy ion bombardment (see Figure 5). These results underscore the robust immunity GaN transistors provide to various forms of radiation found in space.
As well as great robustness to radiation, GaN HEMTs excel in electrical performance, due to their high electron mobility and wide bandgap. The transistors also exhibit a low on-resistance and low input capacitance, ensuring that the figure-of-merit that comes from the product of these two characteristics tends to be more than ten times lower than that of similarly rated silicon MOSFETs.
Figure 5. Gate to Source leakage and Drain to Source Leakage, IGSS, IDSS vs. Fluence at LET =83.
At EPC Space, a joint venture between EPC Corporation and VPT Corporation, we have been developing a product line of rad-hard discrete and modular components for space motion control, as well as other power-related applications. Drawing on EPC’s proprietary Rad Hard eGaN HEMTs, our portfolio of discrete devices provides two packaging configurations: hermetically-sealed devices in thermally-efficient AlN ceramic packages; and discrete devices mounted to AlN ceramic die adapters/‘inteposers’, designed for hybrid applications. Modular devices in our family include single and dual low-side gate drivers; single and dual low-side power drivers, incorporating proprietary GaN-driving-GaN gate drivers, along with power HEMT switching elements and Schottky catch rectifiers; and a half-bridge driver comprised on independent low- and high-side power drivers. All devices have demonstrated radiation performance.
One of the products within this portfolio, the FBS-GAM02-P-R50 module, can be readily configured in a half-bridge configuration (see Figure 6). This module, housed in an 18 pin non-hermetic plastic over-molded package, features low- and high-side power switches, gate drivers and Schottky catch rectifiers, a high-side bootstrap capacitor and diode, an under-voltage ‘power good’ function, and input shoot-through protection.
Figure 6. EPC Space FBS-GAM02-P-R50 in a half-bridge configuration.
Many of the motors that are used in space drive reaction wheel assemblies. This includes the use of three-phase motors to drive spinning masses in the x, y and z axes, to create inertia in one or more of these axes and ultimately control the altitude and position of a spacecraft in orbit. By selectively changing the speed of rotation, and thus the inertia of the spinning mass, it is possible to control the pitch, yaw and orbital position of the spacecraft. To control the three-phase motor, three half-bridge drivers are required per motor. And as three axes require control, nine half-bridge drivers are needed for each reaction wheel assembly system.
To address this motor drive requirement, we have developed the EPC7C006, a three-phase motor demonstration board that utilises the GAM02 as the three-phase control switches (see Figure 7). This board is designed to be either stand-alone, with phases driven by external three-phase digital pulse-width modulation signals, or to interface with the EPC9147A microcontroller interface board – it features a Microchip DSP to provide a pulse-width modulation signal for each phase, based on voltage, current and optional positional feedback. This control board utilises the Microchip motorBench Development Suite, under license to EPC. Thanks to this, designers either control the motor to be driven in the end-application with an existing control system developed in-house, or with a purpose-built control system that interfaces to a computer via a USB connection and GUI interface provided by us or EPC.
Figure 7. EPC Space EPC7C006 three-phase motor driver demo board, which measures 6.50 inch by 5.22 inch.
There’s no doubt that the commercial and industrial activities planned for space, both in orbit and extra-terrestrially, are demanding and exciting. Many motors are already spinning away in space, and it is a sure bet that far, far more will follow. Thanks to our efforts, circuit designers no long need to feel daunted by the task of implementing high-reliability motor control circuits, due to the availability of robust, rad-hard, high-performance discrete devices and modular components for motor drive/control. Our products offer inherent radiation hardness, a trimming of size and weight, and a reduction in losses from heat generation, allowing designers to focus on optimising the electro-mechanical performance of the motor system. Do this, and the biggest benefit of all is keeping the motor system in question on-orbit, or fulfilling its mission elsewhere.