A growing reliance on power electronics
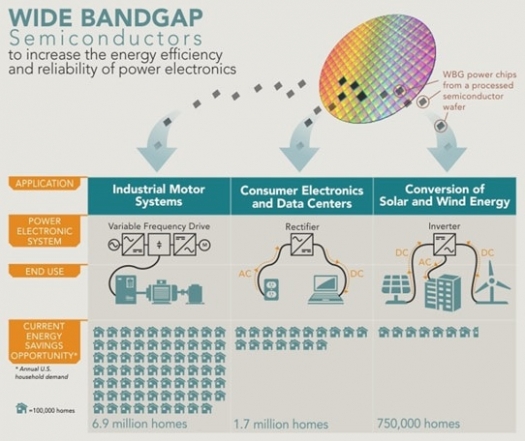
The Next Generation Power Electronics National Manufacturing Innovation Institute will use $70 million provided by the U.S. DOE's Advanced Manufacturing Office to support and manage its programs over the next five years
The share of electricity flowing through power electronics is expected to increase rapidly. By 2030, an estimated 80 percent of all U.S. electricity is expected to flow through power electronics.
Thirty percent of electricity in the U.S. flowed through power electronics in 2005 and in 2030, it's estimated to be 80 percent.
Large Energy Savings
If wide band gap (WBG) semiconductor-based power electronics were to replace the silicon-based power electronics currently used in industrial motor drives, renewable energy conversion, data centres, and electrical consumer products, enough electricity would be saved annually to power at least 9.3 million homes.
Improved Control of Electrons
Current applied to WBG semiconductors will not excite as many electrons across the gap (compared to silicon semiconductors), enabling finer control over the flow of electrons. This and other properties of WBG semiconductors enable faster, smaller, more reliable and efficient power electronic devices.
Industrial Motor Systems use power electronics in variable frequency drives. The potential energy savings from more efficient WBG semiconductors is equivalent to the power used by 6.2 million homes (2014 Potential). Consumer electronics and data centres use power electronics in rectifiers which convert AC power supply from the grid to DC supply for data centres.
The potential energy savings from more efficient WBG semiconductors in this application is equivalent to the power used by 1.3 million homes (2014 potential). Conversion of renewable energy requires power electronics in inverters which convert DC power supply from renewable generation to AC supply to the grid.
The potential energy savings from more efficient WBG semiconductors in this application is equivalent to the power used by 1.3 million homes (Projected to 2040). Note: all potential energy savings figures based on annual U.S. household demand.
Eighty-five percent of savings in industrial motor systems is from market expansion.
Power Electronics: Small, reliable, and energy efficient
Power electronics convert and control electrical power across the grid and in a growing array of products used by industry, consumers, the military, and utilities. Wide bandgap (WBG) semiconductors - the same materials used in LED light fixtures and many flat screen TVs-can improve energy efficiency in the next generation of power electronics while also reducing cost and system size.
WBG semiconductors used in variable frequency drives, for example, increase the efficiency of industrial motor systems and expand the range of motor applications in which these energy-efficient drives are cost-effective.
Moreover, WBG-based power electronics are more compact and reliable - even as they function at higher power loads, operating temperatures, and frequencies than today's widely used, silicon-based power electronics.
WBG: Enhanced capabilities
Semiconductors are materials that can allow electricity to flow more readily than insulators - but less readily than conductors. This property makes semiconductors extremely useful for fabricating power electronic chips that control and convert electrical power (i.e., adjust the voltage, current, and frequency as required by various equipment and applications).
A bandgap is the term used for the amount of energy needed to release electrons in semiconductor materials so that the electrons can move freely, enabling the flow of electricity.
WBG semiconductors have bandgaps significantly greater than those of silicon semiconductors. Electrical current applied to WBG semiconductors will excite fewer electrons across the gap, enabling superior current control and reducing energy losses.
WBG semiconductors, such as SiC and GaN are able to operate at higher voltages and power densities than silicon-based semiconductors, allowing the same amount of power to be delivered with fewer chips and smaller components. In addition, these more powerful WBG semiconductors can operate at higher frequencies, which helps to simplify system circuitry and reduce system costs.
Furthermore, WBG semiconductors tolerate heat better than silicon. As a result, WBG-based power electronic chips can operate in harsher conditions without degrading the semiconductor material. This greater thermal tolerance (300°C vs. 150°C) reduces the need for bulky insulation and additional cooling equipment, allowing for more compact system designs.
Collectively, these performance properties of WBG semiconductors will enable technology developers to continue designing increasingly more compact, efficient, reliable, and affordable power electronics in the decades ahead.
Building more cost-efficient power electronic systems
Semiconductor chips are fabricated by creating complex circuits on a thin, circular wafer (substrate) using a series of iterative processing steps (e.g., oxidising, etching, doping, etc.). An automated approach to these fabrication processes produces multiple, integrated circuits or chips on a single wafer.
These wafers are then sliced apart to create a number of identical "chips." As WBG wafers become available in larger sizes compatible with the automated equipment and infrastructure used by the silicon industry, WBG chip production will scale up substantially.
Chips perform critical power conditioning functions in devices like rectifiers (convert AC electricity to DC), inverters (convert DC electricity to AC), and variable frequency drives (which include both inverters and rectifiers). WBG semiconductor-based devices perform these functions more efficiently, yielding significant energy savings.
Industrial Motor Systems
Motor systems use nearly 70 percent of the electricity consumed in U.S. manufacturing today. Many manufacturers size their motors to handle peak demand, so these motors often use more power than is actually needed. Some large motor systems can use a variable-frequency drive (VFD) to dynamically adjust motor speed to match power requirements and save energy.
More efficient and compact WBG-based VFDs could expand the range of motors in which VFDs are cost-effective. Installing WBG-based VFDs on this expanded range of motors can save enough electricity annually to power 6.9 million homes.
Of this total, savings equivalent to 1 million homes are directly attributable to the installation of WBG-based VFDs. Savings equivalent to an additional 5.9 million homes are due to the expanded range of motor applications made cost effective by WBG-based VFDs, compared to conventional VFDs.
Consumer Electronics and Data Centres
Power converters for data centres and consumer electronics (such as laptops, smart phones, and tablets) account for nearly 4 percent of U.S. electricity use today, and the demand for these facilities and products continues to rise.
The small converter on the cord of your laptop computer, for example, converts the AC power from your wall outlet into the DC power used by your laptop. Similarly, data centres need to convert power to meet the needs of the diverse components of modern data centre systems.
WBG chips will eliminate up to 90 percent of the energy losses in today's rectifiers that perform these conversions. WBG-based power electronics in consumer electronics and data centres can save enough electricity annually to power over 1.7 million homes.
Conversion of Renewable Power
Power generated by renewable wind turbines and solar photovoltaic systems must be converted from DC to AC prior to upload to the electric grid. The WBG chip provides the required conversion in the invertor. More efficient WBG-based power electronics for solar and wind energy conversion can annually save enough electricity to power more than 750,000 homes.
The Next Generation Power Electronics National Manufacturing Innovation Institute will use $70 million provided by the U.S. Department of Energy's Advanced Manufacturing Office to support and manage its programs over the next five years.
This Institute is one of three new innovation hubs announced by President Obama in his 2013 State of the Union address and part of the National Network for Manufacturing Innovation (NNMI). The Institute will establish a collaborative community devoted to wide bandgap power electronics.
It will create, showcase, and deploy new power electronic capabilities, products, and processes that can impact commercial production, build workforce skills, enhance manufacturing capabilities, and foster long-term economic growth in the region and across the nation.