SMC: Swelling SiC shipments with a second fab
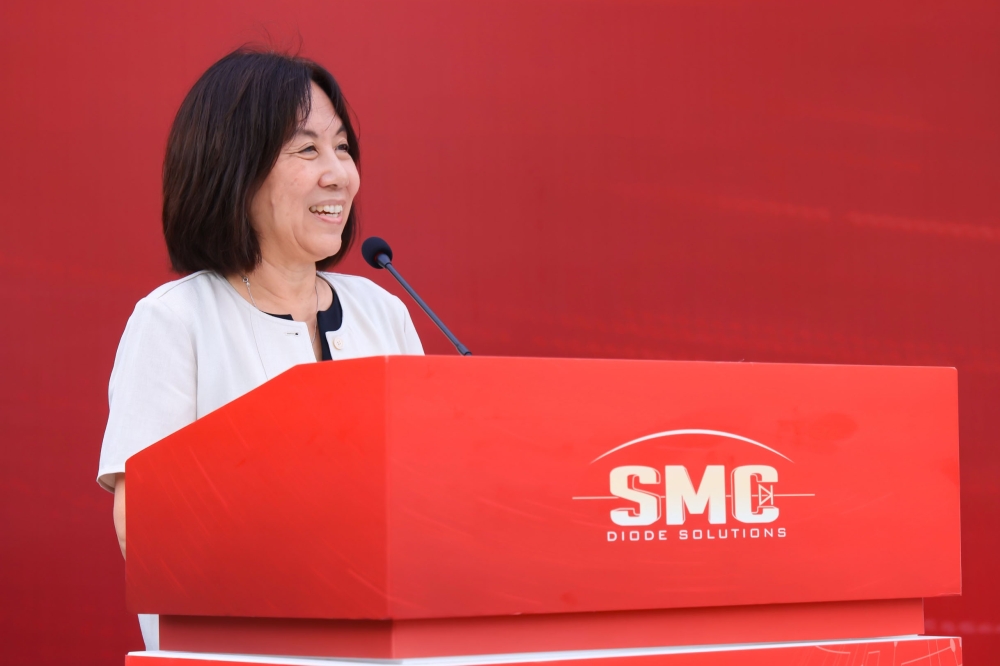
Opening an additional fab in Nanjing will help to grow sales of SMC Diode Solution’s SiC products to around half the company’s revenue.
BY RICHARD STEVENSON, EDITOR, CS MAGAZINE
Within our industry, one of the biggest trends is the growth in sales of SiC devices by companies with a strong pedigree in producing silicon power electronics. Of the current big five in SiC, Wolfspeed is the only player producing just wideband materials and devices, while STMicroelectronics, Onsemi, Infineon and Rohm have branched out into SiC after establishing a strong portfolio of silicon-based power electronics.
This direction of travel is also being pursued by some of the smaller players, such as SMC Diode Solutions, an American-led company that produces silicon and SiC power devices and has just opened its second fab in Nanjing, China. Opening this 300,000 square foot facility, which cost $3 billion RMB (US $410 million) and is creating 300 new jobs, will enable the company to boost production by 1.2 million silicon wafers and 60,000 SiC wafers per year – that equates to more than a quadrupling of the company’s annual output.
Founded in 1997, SMC started considering the expansion of its power portfolio to include SiC products in 2014. Back then, when far fewer producers of these power devices competed for sales, SMC’s chairwomen and CEO Yunji Corcoran reasoned that expanding into this area would enable her small-to-medium-sized company to expand its range of products and potentially target new applications.
At that time, Corcoran considered diversifying into either SiC or GaN. However, she felt that the pioneers of SiC, particularly Cree, offered a better-defined product. If SMC manufactured these devices, Corcoran believed that it would have a great opportunity to sell them to its existing customers, predominantly large power-supply companies. According to her, compared with GaN power devices, those based on SiC are much closer to SMC’s silicon power rectifier family.
SMC started its commercial expansion into SiC with the production of Schottky rectifiers, shipping from 2019 onwards. Beginning its SiC offering with this product made much sense. “We are a silicon diode company,” argues Corcoran, pointing out that by starting with a SiC Schottky rectifier, it’s been easier to find customers for its first range of products.
Once SMC starting working with SiC, Corcoran and her colleagues could see the tremendous potential for the SiC MOSFET.
Today the company produces both classes of power device. Its SiC Schottky barrier diode portfolio has products with blocking voltages from 600 V to 3.3 kV, and a wide range of current ratings, which can include those that target a customer’s particular needs.
The family of SiC MOSFETs is not as broad. There are 1.2 kV MOSFETs with on-resistances ranging from 16 mΩ to 160 mΩ, as well as a recently introduced a 1.7 kV variant. However, there are plans to expand the range. “We are working on the 650 and the 3300 at this moment,” enthuses Corcoran.
Silicon products are dominating SMC’s sales today, with those based on SiC only accounting for 10 percent of revenue. Corcoran attributes this modest but growing proportion to working with large and rigorous customers that are thorough when designing and evaluating prototypes.
Just a small fraction of the products that SMC makes in China are sold on the domestic market. 90 percent of business comes from sales oversees. Accounting for this, Corcoran explains that while her home town is Nanjing, she moved to the US to study and work, and it is there that she acquired her business acumen.
Given current tensions between the US and China, one might expect it’s not easy for a company to have a fab in Nanjing that ships most of its products overseas. But somewhat surprisingly, SMC’s activities have not been impacted by trade wars.
“When the US applied the duties, we were very concerned,” admits Corcoran. “But in the end, it did not decrease our sales much, because it's not that easy to source our product outside China.” However, she thinks the situation may differ surrounding the SiC MOSFET.
SMC’s chairwomen and CEO Yunji Corcoran grew up in Nanjing before moving
to the US to study for a PhD in Materials Science and Engineering at
Stony Brook University. She has held the role of CEO at SMC since its
founding in 1997.
Outsourcing growth
For the leading manufacturers of SiC diodes and MOSFETs, there is a tendency to shift to greater degrees of vertical integration. Now some companies are beginning with the production of SiC boules from powders and concluding with the shipping of packaged devices.
For SMC, there’s little sense in trying to emulate these bigger players. Instead, the company is focusing on what it is good at.
“We are not doing the epi, we're not doing the substrates, and we don't even do the packaging,” says Corcoran, who explains that SMC’s two fabs are used to process epiwafers into power devices.
For the company’s silicon products, there is a plant that can package the chips into modules. In the future, the plan is to use this facility to produce modules from SiC MOSFETs made in-house.
SMC uses suppliers based in China for its SiC Schottky-barrier-diode epiwafers, with Corcoran describing the quality as “pretty good”.
For MOSFETs, a more complicated structure, the local supply is not as strong. “But we’re testing the Chinese substrates,” says Corcoran. “I think they are coming along.”
She explains that SMC is devoting much effort to understanding which kinds of defect impact the MOSFET. Equipped with that insight, the company will be better prepared to assess the quality of Chinese SiC MOSFET epiwafers, and ensure that when they switch to them, there is no reduction in device performance.
According to Corcoran, there are many good reasons for selecting Nanjing for its a second fab. As well as the advantage of being close to the first fab, this location benefits from: strong universities nearby; a good education system; a cost of living lower than that found in the cities on the east coast, such as Shanghai; and plenty of engineers with relevant expertise, partly due to a very large, local TMSC fab.
Today, SMC’s fabs produce devices from 150 mm SiC epiwafers. However, the tools could be converted to handle 200 mm material – that’s a move that is planned when the cost-per-unit-area of the larger format falls.
Another change may be an increase in the proportion of SiC devices produced in the fabs.
“We invested a lot of money in silicon carbide, and I hope we will have more than 50 percent of silicon carbide as our total revenue,” says Corcoran. While sales of silicon devices are steadily increasing, she anticipates far faster growth for SiC products.
As well as shifting the balance of the product portfolio, SMC plans to penetrate new markets. The aim is to expand from simply serving the power supply sector to winning sales in renewable energy markets, including electric vehicles.
With more chipmakers with a silicon heritage now pursuing SiC, the chances that supply will satisfy demand are improving, helping humanity’s efforts to try and curb its carbon footprint.