Researchers develop damage-free etching for gallium oxide
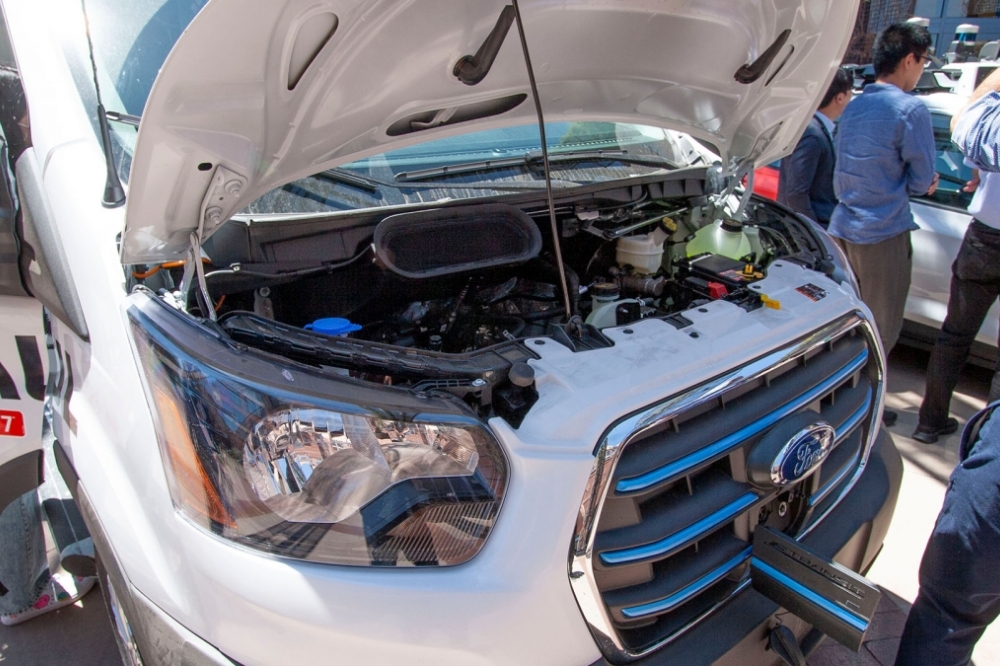
New technique can be completely performed within a MOCVD reactor
Gallium oxide is an emerging ultrawide bandgap semiconductor with great potential for power electronics. However, methods for etching have a problem: they damage the material.
Nidhin Kurian Kalarickal, an assistant professor of electrical engineering at Arizona State University, has solved this problem by developing a damage-free etching process with engineering student Abishek Katta and collaborators from semiconductor manufacturing equipment company Agnitron Technology.
Traditional etching of gallium oxide is done using the standard process of plasma-based reactive ion etching and uses gases such as chlorine and argon. The process involves exposure to energetic plasma, which damages gallium oxide, creating surface and subsurface defects and reducing its power conversion capabilities.
To remedy the damaging methods, Agnitron representatives approached Kalaricka, and discussed developing a new etching process after ASU purchased an MOCVD reactor tool from the company.
“Agnitron wanted to engage with my team, and the company’s representatives were quite interested in the idea of investigating in situ etching using metal-organic precursors,” Kalarickal says.
Kalarickal and Agnitron’s method differs from traditional ones in that it uses the same basic metal-organic compound, triethylgallium, that is also used for the growth of gallium oxide in the presence of oxygen. Other methods use a different material that involves damaging energetic plasma.
When gallium oxide is heated and exposed to triethylgallium in the absence of oxygen, gallium oxide undergoes a chemical reaction, resulting in the formation of gallium suboxide. Gallium suboxide is volatile and easily escapes from the sample surface, resulting in etching.
Kalarickal’s method does not involve energetic plasma, eliminating the damage that occurs to gallium oxide from traditional processes. The new technique can be completely performed within a MOCVD reactor, making it possible to etch and grow gallium oxide without exposure to the ambient environment.
Since the in situ method’s development, Kalarickal and his collaborators have worked on two scientific journal papers related to the project. One has been accepted for publication in the Journal of Applied Physics, while the other is almost complete for submission.
The in situ etching process has already been put into practice, as well. Doctoral students in Kalarickal’s research group are using the method to develop high-performance power electronic devices, charging up the field for an electrically powered future.