The world’s biggest SiC fab
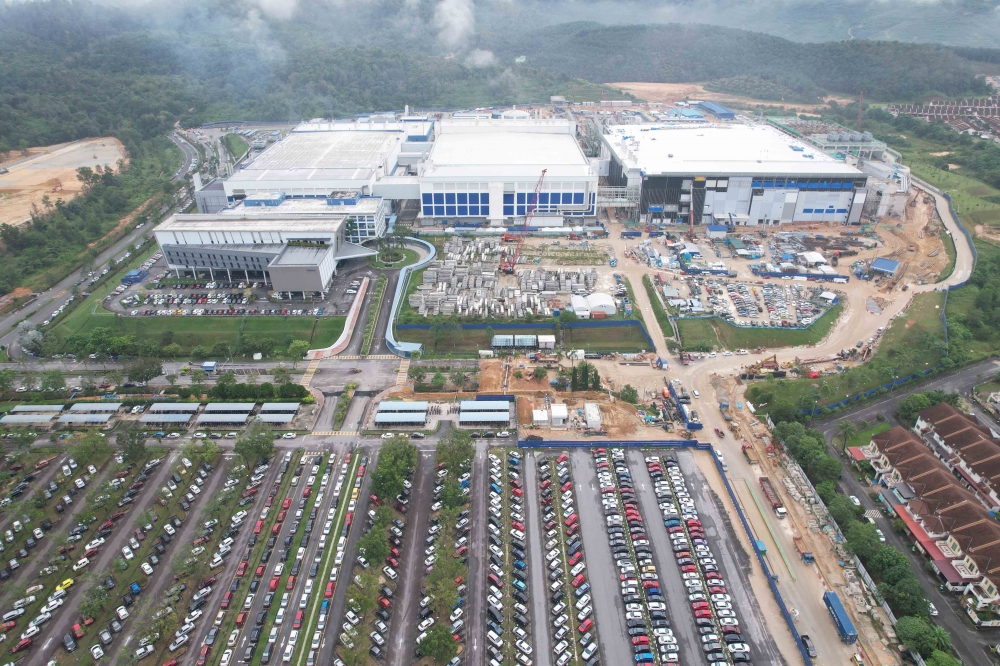
Infineon’s construction of the world’s largest SiC fab, in terms of
both its footprint and its capacity, remains on track for opening in
the third quarter of this year.
BY RICHARD STEVENSON, EDITOR, CS MAGAZINE
Within the SiC industry, much manufacturing takes place in-house. So, when these chipmakers want to increase production, they tend to boost internal capacity. That’s in full flow right now, spurred on by the tremendous ramp in sales of electrical vehicles, which deploy SiC power devices in the on-board charger and DC-DC converter.
One of the companies grabbing the headlines for capacity expansion is the power-electronics giant Infineon, which lays claim to constructing the world’s biggest 200 mm SiC fab, in both size and capacity.
Initially backed by €2 billion of internal funding, plans for the new fab in Kulim, Malaysia, were bolstered last summer with the injection of a further €5 billion for building and equipment. Back then the company announced that the completion of the first phase of this fab remained on track for the third quarter of 2024, a deadline that’s still on schedule, according to Ng Kok Tiong, Senior Vice President and Managing Director of Infineon Technologies Kulim. Over the next five years the completion of the second phase will proceed.
Infineon’s new SiC power fab, known as Kulim 3, is being built next to a pair of its 200 mm silicon fabs. However, even those fabs, constructed in 2006, were not the beginning of off-shoring of manufacturing by the European powerhouse in Malaysia. Through Siemens, which divested Infineon in 1999, there has been investment in Malaysia for almost 50 years, including the construction of a back-end assembly and test facility in another state, Malacca. The combination of fabs in Malaysia gives Infineon end-to end production within the country. In fact, the investment in semiconductor manufacturing is so strong that Infineon has more employees in Malaysia than any other country, including Germany.
According to Ng, one of the reasons why Infineon decided to expand its SiC production capability by building a third fab at Kulim is that this offers a very fast way to ramp capacity. That’s partly because compared with other countries, approval can be granted for construction to take place during more hours of the day, thanks to local labour law.
One difficulty with building any new fab is winning approval for the water and electricity that’s supplied to the site. Ng believes that this has been granted quickly for Kulim 3. Building a new fab next to existing ones helps, but in addition to that, Infineon benefits from having a large, welcomed presence in Malaysia.
“We are working very well with the government, with MIDA, which is the government agency for investment,” remarks Ng, who adds that they get a lot of attention for any support that’s needed.
Ng says that equipment will start being installed in Kulim 3 from April 2024, with production of SiC devices slated for the second half of that year.
Engineers at this fab will carry out all aspects on front-end processing, including production of SiC substrates from boules provided by five suppliers – two from China, two from the US, and one from Japan. Helping increase the margins associated with this process is the Cold Split technology that Infineon acquired from Siltectra in 2018. “With this new technology you can reduce some of the losses of the raw material,” says Ng.
Construction of the 200 mm SiC fab is expected to create 900 jobs, with the vast majority taken by local people. To help with the training of Malaysian engineers, many are sent to Infineon’s other SiC fab, located in Villach, Austria. In addition, experts from there visit the facility in Kulim.
To help attract the best local talent, the Kulim fab works very closely with local universities and polytechnics by offering placements for internship and final year projects. Ng and his colleagues have found that due to need for very specific expertise, even engineers graduating after a four-year programme can take 8 months of training before they can start making meaningful contributions. So, to avoid this delay, a programme has been introduced, with students spending time at the facility and having an engineer at the fab as a mentor. “By the time they graduate, they are already effective, because they know SPC, they know how to do the DoE, and things like that,” says Ng.
Helping Infineon commit to investing in Kulim 3 are a number of design wins totalling €5 billion. They are roughly a 50-50 split between the electric vehicle and industrial sectors, with the latter a mix of solar and storage industries.
The plan is that by the end of this decade, production at both the Kulim and Villach sites will account for a 30 percent share of the SiC power market, which by then will be worth about €20 billion.
While emphasis is initially on SiC at Kulim 3, efforts are also underway to develop GaN products at this site. The first steps towards this, now underway, involves the qualification of the growth process.
Based on all the plans for wide bandgap semiconductors at Kulim, there’s no doubt that the long-term relationship between Infineon and Malaysia will only get stronger throughout this decade and beyond.
Ng Kok Tiong is Senior Vice President and Managing Director of
Infineon Technologies (Kulim) Sdn. Bhd., which is Infineon’s first and
only wafer fabrication plant in Asia. Ng is also currently the Chairman
of The Semiconductor Fabrication Association of Malaysia.
Main image: Construction of Kulim 3, the world’s biggest 200 mm SiC fab, is well underway.