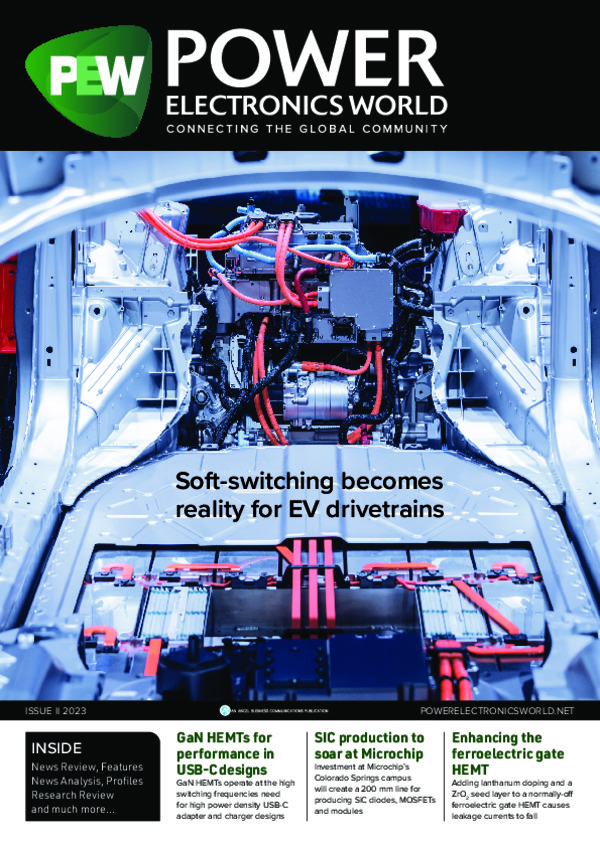
Soft-switching becomes a reality for EV drivetrains
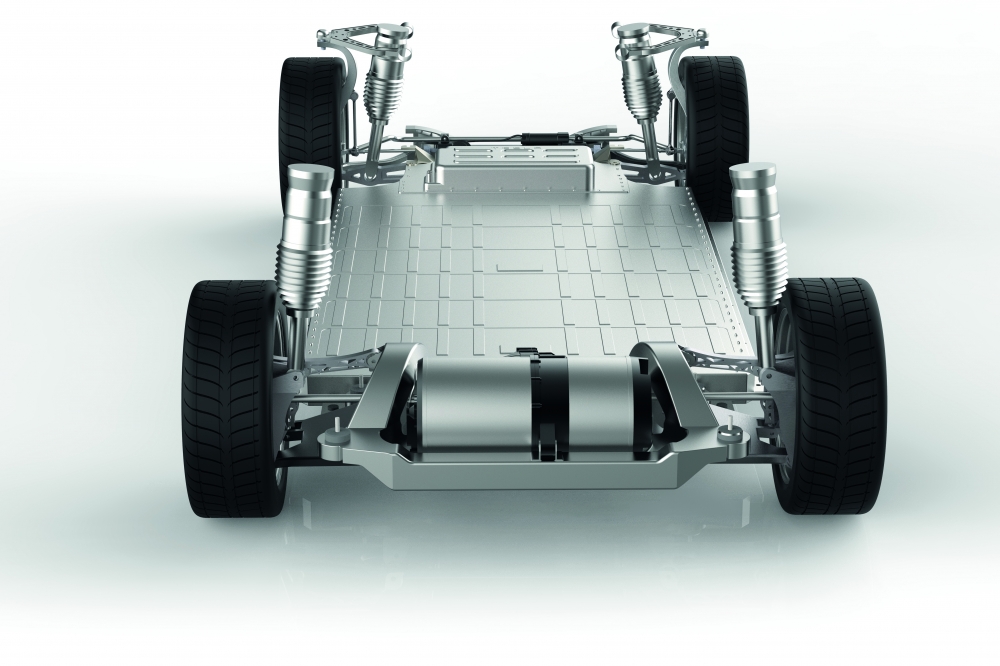
Soft-switching at high frequencies used to be impractical. Now, a new approach, using a forced-resonant topology controlled by AI, is delivering inverters that are 98.5 percent efficient at 5 percent load, and 99.57 percent peak.
Bruce Renouard, CEO of Pre-Switch Inc, explains the benefits.
Transportation is in a period of great change as electrification asserts itself as the preferred technology for a greener, sustainable future. But the automotive internal combustion engine has enjoyed over 100 years of heavy investment, development and refinement.
EVs, by contrast, are still emerging and – in many ways – have some catching up to do. Limited range is one of the major concerns for people when they look into EVs. Charging time is another. Both these factors demand that EVs must be as efficient as possible. Which is one of the main reasons why the EV industry is so interested in soft-switching, which promises very high efficiency across the full load range.
Various soft-switching architectures have been discussed for many years, but until recently, soft-switching at high frequencies has been impractical. Now, a new approach, using a forced-resonant topology controlled by AI, is delivering inverters that are 98.5 percent efficient at 5 percent load, and 99.57 percent peak, resulting in increased EV range of up to 12 percent.
These performance figures are part of the reason why one former Audi EV drivetrain designers believes that “in future, all EV inverters will need to use soft-switching”.
Figure 1a & 1b
What is ‘soft-switching’?
Let’s start by defining ‘soft-switching’. There are basic approaches to switching transistors on and off. These are termed: ‘hard- and soft-switching’. Hard-switching turns the target transistors on and off directly. Although this is a very simple design, it leads to switching losses when transistors turn on and off in the presence of a voltage as shown in Figure 1a .
These losses are higher in high-voltage transistors employed in EVs, and there are also other issues. Hard-switching generally requires a lower switching frequency, EMI is increased and the size and weight of components such as DC link capacitors can increase to the point where they occupy up to 60 percent of the inverter volume. These characteristics result in reduced efficiency and increased system cost.
In contrast, soft-switching is achieved when the transistors are turned on and off when there is no voltage present (zero voltage switching) as in Figure 1b. This is achieved using a self- or forced-resonant circuit to ensure effective transistor commutation timing. The result is that switching losses are virtually eliminated, EMI is reduced and efficiency is significantly increased. However, soft-switching has never been perfected for isolated AC/DC and DC/AC power converters, so consequently this topology has been limited to non-isolated power converters with low input voltage and output load range.
The challenge has been how to ensure that the transistors always switch on and off at the precise point when voltage is zero, given many varying factors, such as input voltage, output load, device tolerances, and temperature changes. This is the essence of the Pre-Switch breakthrough: artificial intelligence (AI) is used to monitor all these variables and adjust the timing on a cycle-by-cycle basis to achieve true soft-switching.
Figure 2.
Using AI to resolving timing calculations
The Pre-Switch topology for soft-switching is a variation of the Auxiliary Resonant Commutated Pole (ARCP) soft-switching converter topology. At its most basic, ARCP is a conventional inverter topology with an auxiliary circuit that helps soft-switch the main inverter (Figure 2).
The auxiliary switches are activated before the main power output switches, and generate a current in the auxiliary inductor that is used to induce the condition required to soft-switch the main inverter switches. The auxiliary switches are turned on and off at zero current while the main switches are switched at zero voltage.
The sophisticated, embedded AI, developed by Pre-Switch, dynamically solves all complex timing calculations demanded by changing operating conditions, and resolves the previous limitations of ARCP soft-switching. The control algorithm can drive any type of power switch and is ideally suited for all power switching technologies including silicon-based IGBTs and MOSFETs, gallium nitride (GaN) and silicon carbide (SiC). The Pre-Switch topology enables drivetrain systems based on with industry standard IGBTs and MOSFETs to equal to surpass state-of-the-art wide bandgap-based power components (SiC & GaN).
An animated sequence of 20 1µs screen captures (Figure 3) provides a simplified explanation of the Pre-Switch AI, showing the algorithm actively learning from initial start-up with unknown conditions, then subsequently optimizing and adjusting the timing necessary to ensure that a PWM input generates a current ramp to simulate the first part of a sine wave output. The GIF demonstrates how the AI is works with Pre-Switch’s Cleanwave 200kW inverter reference to bi-directionally convert 800VDC to three-phase AC at power levels of up to 200kVA with a switching frequency of 100kHz at 99 percent efficiency levels.
Double pulse test data obtained from the Cleanwave inverter demonstrates that the Pre-Switch soft-switching platform – comprising the Pre-Drive3 controller board powered by the Pre-Flex FPGA, and RPG gate driver board – reduces total system switching losses by 90 percent or more.
Upon commencement of the initial switching cycle (0), the Pre-Switch AI controller assesses multiple inputs to determine what mode the system is in, and then makes a safe but non-optimal estimate of the resonant period needed for soft switching. During the next switching cycle (1), all AI inputs and resulting outputs from switching cycle 0 are precisely re-measured and analysed. A second conservative resonant timing period, similar to switching cycle 0, is issued.
In follow on switching cycle (2), the AI algorithm is now quantitatively-confident and able to predict the optimized resonant timing to ensure full soft-switching – thus minimizing losses in all aspects of the system. Then in switching cycle 3, the AI compares system inputs and results from previous switching cycles and adjusts the resonant timing to fully optimise soft-switching with the increasing load current. These inputs and outputs are stored with the previous switching cycle inputs and resulting resonant timings to improve accuracy and system optimization. In subsequent cycles, soft switching accuracy continues to be optimized, stored to and compared to desired results necessary to maintain accurate forced resonance soft switching. Changes in system temperature, input voltage, output load current, and device degradation are all accounted for and optimized within the AI algorithm, which is being continuously updated.
The dynamic, soft-switching control AI is delivered in Pre-Switch’s Pre-Flex programmable ICs. By incorporating a remote boot code on the chip, Pre-Switch can update the AI at any point during the life of an EV or other product, ensuring that performance is always optimal. Pre-Flex ICs also now include an embedded digital oscilloscope, Deep View, enabling designers to diagnose exactly what is occurring remotely, and then make adjustments in-situ. Traces can be recorded and exported out to see how the system is performing. If there are any issues, Deep View enables developers to understand why, so that actions can be taken. In future, preventative maintenance programs may be able to be implemented, using the feedback from Deep View and the remote programming capability.
The practical implementation of soft-switching is resulting in huge drivetrain benefits.
Figure 3.
Soft-switching inverter benefits
Soft-switching effectively eliminates switching losses for wide bandgap (WBG silicon carbide + gallium nitride) transistors, and reduces IGBT switching losses by approximately 65-80 percent, resulting in increased efficiency. Specifically, efficiency is improved in the low operating points for inverters where switching losses dominate total losses. The result is an inverter with higher peak efficiency, higher average efficiency and higher low-load efficiency.
The elimination of switching losses also reduces cost by allowing designers to pass more current through a transistor with the same transistor loss budget. This is possible because the transistor is no longer dissipating switching losses as well as conduction losses. There is also a second order improvement in transistor conduction losses because the transistors are operating at lower temperatures. Both factors combine to reduce cost and size of an inverter.
The elimination of switching losses also means that inverter switching speeds – which today are limited to slow (10-15 kHz) frequencies in order to maintain efficiency – can be run 5-10X faster (50-100kHz) with the same or higher efficiency. Pre-Switch’s higher switching frequencies have profound inverter and motor benefits. They include: a high-quality sine wave sent to the motor which improves motor efficiency; a reduction in the DC link capacitor size and cost by up to 90 percent; the elimination of audible noise that can be heard by human ears; and reduced common mode noise in the motor between the rotor and stator which is known to ruin motor bearings.
Soft-switching enables designers to build a lighter and lower cost inverter, as discrete transistors can be used instead of heavy and expensive power modules.
Lastly, Pre-Switch technology virtually eliminates EMI because each transistor is turned on and off with no voltage or current present.
Soft-switching motor benefits
A soft-switching inverter reduces sine wave output distortion by 10 times, enabling motors to run more efficiently. In a conventional hard switching design, the output ripple current of the half-bridge circuit switching back and forth at 10-15 switching events per fundamental frequency causes a significant level of distortion. The distortion is effectively an induction heater in the motor coils and does no useful work. Soft-switching minimizes this ripple by switching 10 times faster. The reduced-distortion fundamental sine wave to the motor improves motor efficiency predominantly at lower RPM and lower torques which is where EV’s are driven and increases EV range.
The second benefit of the Pre-Switch soft-switching architecture is that inverter dV/dt is configurable with a free lossless dV/dt filter that is part of the architecture. Reducing dV/dt improves motor reliability and reduces motor winding insulation allowing higher power density motors. Due to the fast edge speeds of WBG (SiC; GaN) transistors, high dV/dt is traded off for reduced switching losses. But high dV/dt speeds of above 10-15V/ns can cause insulation damage. Inverter designers in the past accommodate these excessive dV/dt speeds by adding extra insulation in the motor. This approach has the adverse effect of reducing motor power density and increasing motor costs. In contrast, the Pre-Switch architecture slows edge speeds but allows increased switching frequencies, eliminating the problem of high dV/dt speeds and reducing the insulation required.
Faster switching speeds mean that motors can be spun faster, so for some applications, a lower cost, lighter and higher RPM motor can be used. The final benefit for motor design is that because Pre-Switch-enabled systems switch so fast, low inductance motors can be used which have the benefit of being smaller and lighter and lower cost. This is particularly suitable for applications such as electric aircraft, where designers are trying to reduce the amount of iron in the motors to keep weight to a minimum.