Strategy Analytics examines the on-going automotive power IC shortage
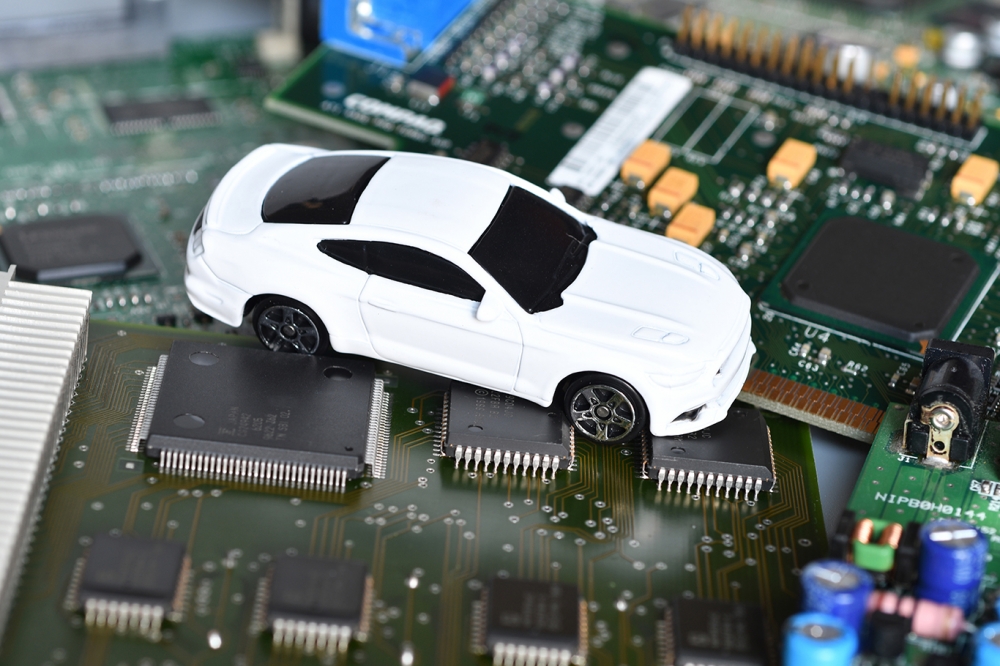
Shortages of automotive semiconductors including power electronics
component-level devices and SoCs led to production shortfalls, idled
workers, price hikes and empty sales lots throughout 2021—issues that
persist into 2022. Power Electronics World asked Strategy Analytics’
Asif Anwar to offer a second quarter update and explore the latest
developments that continue to affect global transport markets.
By Asif Anwar; Director; PBCS; Strategy Analytics.
Semiconductor supply was constrained in 2021 as the automotive industry competed with sharp increases in demand from mobile, consumer electronics and other end markets. The semiconductor shortage was further impacted by several other events including an earthquake in Japan, snowstorms in Texas, a fire at a Renesas facility and a severe drought in Taiwan.
Despite these challenges, front-end semiconductor production started to normalize, but the second half of the year was characterized by headwinds at backend processing facilities as a resurgence in COVID-19 cases there and at R&D operations in Malaysia, India and Taiwan hampered the ability of the automotive semiconductor industry to meet ongoing demand.
The combined impact of semiconductor shortages in general, combined with several other events (snowstorms, droughts, fires) served to limit the much-vaunted recovery in light vehicle production. Major OEMs steadily increased the frequency at which they reported adjustments to their production schedules during 2021, citing the ongoing impact of semiconductor shortages. Even those companies that were initially better prepared, e.g. Toyota, have continued to regularly advise of adjustments to their production lines because of the semiconductor shortage and other material constraints. The situation in Japan was also recently impacted because of an earthquake on March 16 which reportedly impacted the operations of a range of companies including Toyota, Nissan, Kioxia, and Renesas.
The frequency of announcements related to production adjustments declined as OEMs adjusted to the supply constraints. Alongside this was also an acknowledgement that OEMs did not fully appreciate the intricacies of the semiconductor supply chain. This has led to major OEMs publicly announcing deals with major semiconductor suppliers.
The stunted growth for global vehicle production in 2021 because of these semiconductor shortages has been in sharp contrast to the robust financials being reported by automotive semiconductor suppliers through 2021. This is reflected in rising backlogs with suppliers continuing to run at capacity to fulfil the robust growth in automotive semiconductor demand. The combination of strong demand and constrained supply also translated into semiconductor pricing increases. Current modelling predicts a slowing down in price increases from 2023 onwards with ASP year-on-year declines starting to see normalized rates of decline from 2028.
This will be tied with COVID-19 impacts lessening as more of the global populace is vaccinated and an assumption that further variants will have less of an impact on those vaccinated, easing the pressure on hospitals and reducing the requirement for lockdowns. On the other hand, it is to be noted that China is still maintaining a ‘zero tolerance’ approach, which at the time of writing has resulted in major cities, e.g. Shanghai, being put into lockdown; this is having an impact on vehicle production with more notable effects being reported in the second quarter of 2022.
It is notable that there are other challenges that will impact vehicle production in 2022, not least of which is the Russia-Ukraine conflict. As well as the effect on global vehicle production because of OEMs pulling out from Russia, the automotive semiconductor supply chain is having to deal with other factors. This includes the sourcing of raw materials such as iron and steel, the production and supply of wire harnesses, and the production of noble gases used in semiconductor manufacturing will also pose broader challenges to vehicle production. We believe these effects will be temporary as the OEMs, Tier 1s, automotive semiconductor suppliers and the rest of the supply chain adjust their sourcing arrangements. However, this will be coupled with a drop in consumer confidence as inflationary pressures bite into vehicle sales. This will translate into a slower recovery trajectory in 2022.
Semiconductor shortages will continue into the second half of 2022, but there is an inherent assumption that supply-demand dynamics will start to normalize towards the end of the year. While noting the potential for excess inventory build, most automotive semiconductor suppliers have entered long-term supply arrangements with their customers, and in many cases, these are NCNR (non-cancellable, non-returnable) agreements which provide a certain measure of protection.
We also expect that the pricing for strategic components that support the move towards electrification as well as associated trends of ADAS/autonomy, connectivity, domain/zonal and centralized architectures will not see a return to the same demands for year-on-year price declines as traditionally observed for mainstream automotive components. This should further help insulate suppliers from the risks of excess inventory, avoiding a false slowdown in 2023 and 2024.
In conclusion, the much-vaunted recovery in vehicle production failed to materialize in 2021, and the recovery in 2022 will also be more muted than originally forecast. Ongoing waves of COVID-19, coupled with risks to the supply chain due to material shortages and a decline in consumer confidence represent challenges and risks. Nonetheless, the industry move towards electrified platforms will underpin growing semiconductor content per vehicle and maintain growth for the automotive semiconductor industry.
Automotive sector trends and opportunities
Power Electronics World Technical Editor Mark Andrews asked Strategy Analytics Director Asif Anwar to examine the most recent developments affecting the on-going light vehicle semiconductor shortage, exploring where consumer demand and OEM production intersects with a finite supply of vital components including power ICs.
MA: How are semiconductor manufacturers supporting their automotive customers in early 2022 compared to 2021 and 2020?
AA: I wouldn’t say that there is a measurable difference with the way that semiconductor manufacturers are supporting their automotive customers in 2022 compared to 2020 and 2021. Obviously, in 2020 and 2021, the automotive semiconductor suppliers were playing catch-up, and as highlighted, dealing with multiple issues that were beyond their control. What we are seeing is the direct relationship between OEMs and semiconductor suppliers becoming more pronounced, as OEMs recognise the strategic importance of maintaining sourcing arrangements for key components. This is helping semiconductor manufacturers to better plan their output to meet the needs of the automotive industry as they have greater insight into the demand outlook.
MA: Has automotive IC production continued to increase?
AA: The automotive semiconductor makers ramped up extra capacity in 2021 to meet demand. In many cases this was coupled with longer term actions, some of which were already in place and resulted in the opening of new facilities, e.g., Infineon, Bosch, Wolfspeed, etc., as well as ongoing investments in new capacity, e.g., TI (Texas Instruments). The foundational actions have already been taken and 2022 will start to see the results from these actions rather than being a year away.
MA: What are current production levels and revenues (2022) compared to 2021, 2020 or even 2019?
AA: Depends on the metrics being used. What we have observed is that semiconductor companies have continued to increase their revenues in the first quarter of 2022 by an average of 8% (quarter-on-quarter), suggesting that demand remains strong overall.
MA: Are some power device shortfalls worse than others, and if yes, which areas seem to be the most problematic?
AA: In the area of power devices, there is a growing demand for wide bandgap semiconductors with SiC penetration growing strongly, followed by GaN. This is the area that is being focused on by the automotive semiconductor suppliers and we see this reflected in the investment strategies of the major manufacturers. This includes signing sourcing deals for materials as well as making investments that will translate to vertically integrated capabilities so that they can offer material production through to packaged modules.
MA: Is automotive production being affected by other issues besides a lack of some ICs / SoCs, such as supply chain gaps, higher component prices, materials shortages, or the move away from conventional power plants to EV drivetrains?
AA: Yes, as highlighted above, there are several factors that are impacting automotive production besides the supply of semiconductors.
MA: What is the latest picture on when power electronics component production could match demand?
AA: The automotive semiconductor suppliers are making the requisite investments to keep pace with demand, but it is fair to say that we are only at the beginning of the cycle of investment needed as the market moves towards electrified platforms with an emphasis on fully electric vehicles. By 2029, we see electrified vehicles (mild hybrid, full hybrids, plug-in hybrids and battery electric vehicles) accounting for around 50% of global vehicle production. The market will accelerate towards battery electric vehicles as the government mandates, charging infrastructure and consumer knowledge and preference converge around this platform, and this will dictate the demand for power semiconductors and associated investment strategies.
MA: Are there other power electronic devices besides automotive ICs that are in short supply, such as devices intended for household appliances, photovoltaic systems, consumer electronics or other applications?
AA: This is not an area that I cover, but I’m not aware of any major issues related to supply. Household and consumer electronic applications are making use of GaN-on-Si technologies. The underlying Si-based production can meet ongoing demand and we see this reflected in the financials and milestone announcements of companies such as EPC, Navitas, GaN Systems, etc. For higher voltage/higher power applications including renewables, transportation etc., this demand is being met by both Si IGBT and SiC MOSFET technologies and I would suggest that supply is probably sufficient to meet demand given the comparatively lower volumes in these markets.
MA: Are there indications that auto makers (and other manufacturers suffering from a lack of power ICs,) are changing designs or making other accommodations to keep operating?
AA: Automotive OEMs adopted a number of strategies to address the challenges associated with semiconductor and other material shortages. This included:
• Allocation of semiconductor and other resources to production lines focused on the most profitable and/or high-volume brands and nameplates.
• Ongoing reduction in shift hours.
• Vehicles produced but with final finishing delayed until certain components are secured.
• Vehicles produced with certain non-critical components missing that allow a vehicle to be finished with the final production vehicle noting a minor reduction in aesthetics, performance, or fuel economy.
• Temporary shutdown of production lines.
We’ve also seen OEMs now selling and delivering vehicles to the end customer with certain non-critical features missing. In these cases, the customer will then be contacted and asked to return to a dealer to activate the functionality once the components are available. We also see a move away from designing application specific standard parts, which will allow a MCU, for example, to be used across several applications in the vehicle rather than being consigned for a particular use. This provides greater flexibility and the practice is being adopted by both semiconductor suppliers and their customers.
We also see the adoption of more centralized software driven architectures being accelerated. This moves away from the distributed E/E architectures that have been employed by the industry for decades, and potentially allows for the number of ECUs to be reduced, as non-critical functionality can be virtualized in software and processing requirements uplifted into more power SoCs. This move towards use of domain controllers and zonal architectures is not expected to have a significant impact in reducing component demand in the short-term. But we see its use accelerating as the new platforms, which will by default be electrified, adopt these new E/E architectures almost exclusively.