
Unconventional electroplating techniques can improve performance
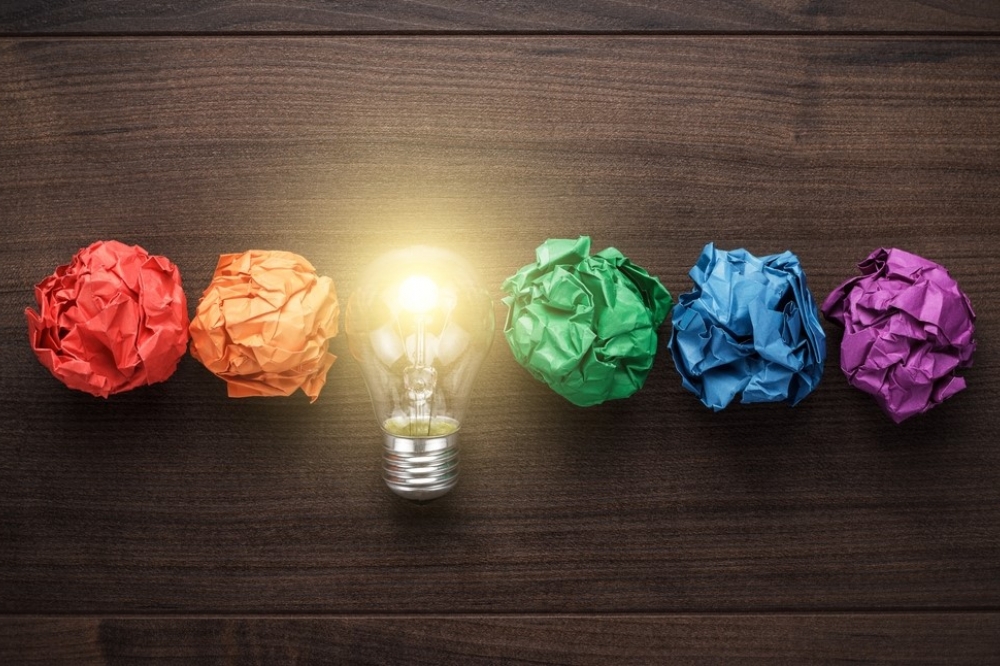
Almost six decades ago Intel cofounder Gordon Moore postulated that processors would evolve regularly to double their transistor count, thereby enabling better performance and lower costs. Whiletraditional Dennard scaling held true for decades, its theoretical limit is fast approaching. The electroplating experts at ClassOne Technology demonstrate a new ‘More than Moore’ pathway.
By Cody Carter, Product Engineer, ClassOne Technology and Stan Wright, Manager, Compound Semiconductor-WLP, MacDermid Alpha
ClassOne Technology has built its business around electroplating innovation, demonstrating that ‘More than Moore’ next-generation technologies do not require ever-shrinking node sizes and exceedingly complex metallization schemes. Today, the company is rethinking fundamental electroplating design to address emerging requirements. Its latest discovery reveals that industry has just scratched the surface of what electroplating can do for power ICs and many other applications.
The Past & Present of IC Tech
The dawn of Moore’s Law in the 1960s recognized a trend in the semiconductor industry – namely, that MOSFET devices doubled in performance every year. Moore then predicted that they would continue to do so at least for the next decade. As semiconductors grew in use and value, manufacturers were able to exponentially improve performance through scaling ever-smaller, further increasing their use and value; this pace of advancement would continue for decades to come, creating two key development trends that have not necessarily been as beneficial to the rest of the semiconductor industry.
The first trend is the way in which technology was driven to development. Because device manufacturers have been primarily focused on scaling logic and memory devices, technology development was dedicated to the specific bottlenecks that hindered this scaling. As a result, certain technologies, such as lithography, received intensive development; other technologies considered adequate for use in this type of manufacturing received less development; and technologies not involved in logic and memory (like gold electrochemical deposition) received significantly less development.
Figure 1. The rate of many device performance metrics has stagnated in recent years.
The second trend, specifically for equipment manufacturers, was that complexity was added to the systems to appease this particular corner of the industry. On electroplating systems, for instance, hot entry and multiple anodes were developed for damascene electroplating to counteract the effects of the high resistance of a very thin seed layer.
In the past decade, however, Moore’s Law has been approaching what appears to be its practical limit in terms of making smaller nodes, as seen in Figure 1. Simultaneously, the compound semiconductor industry has exploded in diversity with the advent of high-voltage power devices based on gallium nitride (GaN) and silicon carbide (SiC) and high-frequency devices based on indium phosphide (InP). This has led equipment manufacturers, chemistry vendors, and process engineers to revisit these trends to (1) focus on underdeveloped technologies and (2) question whether the technologies they made to enable the frenzied growth of Moore’s Law are best suited for this diversity.
To this end, ClassOne Technology and MacDermid Alpha have partnered with their mutual customer, a leading U.S.-based leader in RF device manufacture, to revisit the fundamental reactions occurring in an electroplating system with the goal of attaining better performance from their current process. The outcome was a simple, counterintuitive modification to an existing electroplating reactor.
Figure 2a. Ion concentration varies from the bulk chemistry within the diffusion layer during electroplating.
Figure 2b. Increasing agitation at the anode or cathode shortens the diffusion layer, improving ion concentration curves.
Getting Moore from Less
Like equipment vendors, chemical vendors were focused on improving their chemistry performance in order to keep up with the incredible growth of the semiconductor market. For electroplating, copper has been the primary metal choice for interconnect applications, and for that reason it has historically been one of the technical bottlenecks for successive technology nodes. By plating physics alone, faster deposition will occur at areas with shorter diffusion distances. Because of this, additives were developed and refined to enable varied plating rates dependent on the topography of the wafer surface.
Suppressors move through solution slowly but attach quickly to the wafer surface. Accelerators move quickly but attach slowly. When paired together, suppressors quickly adhere to the higher topography of the plating surface, preventing accelerators from doing so. However, diffusing faster, accelerators can move quickly into the lower topography of a damascene structure or a via and attach to the plated surface there. Levelers then prevent undesirable bumps from forming on the plated surface. These additives have overcome the natural physics and now allow faster plating in areas with greater diffusion distances. The result is uniform deposition on non-uniform seed.
This has been an enabling approach for copper electroplating baths, but other processes, such as gold electroplating baths, have not benefited from this development. Additionally, gold electroplating faces other disadvantages in that it is difficult to stabilize in solution and has very slow diffusion rates. Cyanide-based baths have been the historical standard for gold electroplating. The gold-cyanide complex is relatively stable but does not substantially benefit from high concentrations of gold in solution. More recently, gold sulfite baths have become more popular due to safety concerns with cyanide-based baths and because they allow for higher gold concentrations (and, therefore, faster plating rates). Gold sulfite baths have their own disadvantage, as the sulfite that complexes the gold ion in solution slowly oxidizes over time, making it less stable than its cyanide predecessor.
Compared with copper plating, gold plating is very expensive. The integration of both electroplated metals depends on uniformity to increase throughput in downstream processes (such as CMP). Since gold is very expensive, not only does non-uniform deposition require longer downstream processes, but costs add up in loss of the metal itself, and metal losses are especially egregious when gold is involved. While slower deposition rates can provide better uniformity, it can also cost semiconductor manufacturers by lowering throughput of their electroplating process.
Figure 3. By flowing above the anode, the boundary layer at the anode on the Solstice is increased.
The Problem
For the customer in our case study, electroplating throughput is essential. Years ago, the company developed a process using a legacy cyanide-based soft gold chemistry from MacDermid Alpha that allowed them to meet throughput by running the bath at a current density four times higher than nominal by using semiconductor style fountain plating equipment vs. a traditional rack plating wet bench. One downside of running the bath in this manner is that the bath efficiency (that is, the amount of gold deposited per ampere) would rapidly decrease, then stabilize for a period of time before it needed to be replaced. Since the efficiency is measured by the amount of gold plated per amp, the current was increased so that the plating time for each wafer did not change as the efficiency decreased. This method, though unconventional, proved to be a stable solution. When the customer decided to replace their existing electroplating equipment with ClassOne’s Solstice single-wafer platform, an issue arose in which the electroplating baths now experienced an even more rapid decline in efficiency. Instead of six months, the bath now only lasted two weeks – an unsustainable rate for production purposes.
Several potential solutions were deemed impossible from the outset. Reducing the deposition rate into a lower current density range of the chemistry would require the company to quadruple their electroplating tools to make up for the lack of throughput. Moving to a sulfite-based bath, which would allow them to maintain throughput without detriment to the chemistry, would require an extensive requalification process. The last option, then, was for the three companies to collaborate to determine the root cause of this incongruity between the two electroplating systems.
Figure 4. Modifying the Solstice reactor to affect the anode diffusion layer greatly improved performance over that of the initial Solstice GoldPro reactor configuration, as well as the previously existing tool.
The Process
The first step was creating a model in which we could account for all differences between the two systems – not only physical differences, but even the way they were used in the fab. This included any detail that would pertain to the electroplating reaction, such as the power supply used, fluidics, possible contamination, the way the bath is managed, the product splits between each tool, and even the geometry of the reactors. Overall, 39 individual possible differences were identified, initiating months of troubleshooting to eliminate these possibilities through deliberate testing. What we found would challenge our assumptions regarding fundamental electroplating reactions.
The particular electroplating fundamental in this case is that of the diffusion layer. The liquid immediately proximal to the wafer surface is stagnant relative to the wafer. As agitation of the liquid near the wafer surface is increased (by wafer spin, flow, or paddles), this diffusion layer thins, but it does not disappear. Since this liquid is stagnant, the only way for ions to cross it is by diffusion. The rate of diffusion of a particular ion is dependent on its size and the electromotive force applied by the electric field.
Figure 2a shows the impact of ion concentration at the electrode due to the diffusion layer. The closer to the anode, the higher the concentration of ions; the inverse is true for the cathode. Figure 2b shows how agitation reduces the size of the diffusion layer and therefore affects the availability of ions at the electrode surface for a given current density (depletion rate of ions).
In an electroplating reactor, both the cathode and the anode have critical diffusion layers. As electrochemical reactions occur at the surface of these two components, plating performance (in terms of rate, efficiency, deposited metal uniformity, etc.) is highly reliant on the thickness of the diffusion layer. At the wafer (cathode), a thinner boundary layer allows better access of the ions in the bulk of the fluid with the surface of the wafer, thus allowing faster deposition rate performance. The anode side of the electrochemical cell has its own challenges. In electrochemical processes like traditional acid copper, the anode is soluble, meaning the ions in the bath are supplied by the oxidation reactions on the anode. As the metal atoms from the anode surface oxidize and go into solution, removing them from the anode surface more quickly is desirable as it allows more sites for the oxidation process to occur.
When comparing this example to the customer’s electroplating process, we assumed that an insoluble anode used in gold electroplating processes (where the ions to be replenished are supplied as a soluble salt, not by the anode) would follow similar logic. Since ion concentration within the anode diffusion layer for an insoluble anode is not a controlled parameter (overlooking other reactions at the anode, such as evolution of hydrogen or reactions with electrolyte salts), we thus deprioritized one item that had been on our model since the beginning: the fluid path at the anode.
Figure 5. The competing reaction becomes less efficient with the increased diffusion layer at the anode.
The Solution
The Solstice electroplating system flows chemistry into the reactor directly under the anode. It then flows around it and up to the wafer. On the legacy tool, however, flow comes into the reactor well above the anode and then up to the wafer. By traditional understanding, this was undesirable and not worth putting energy into when there were so many other possibilities.
However, having eliminated all more likely possibilities, we were left with this one difference. We stuck to our problem-solving protocol and made a simple modification to the Solstice reactor to flow the chemistry into the reactor above the anode, as shown in Figure 3. The result was not only a remediation of the short bath life on the Solstice, but a dramatic improvement over the legacy tool’s performance, as shown in Figure 4. While a traditional understanding of the diffusion at the wafer remains intact, this testing has greatly challenged our understanding of its role for inert anodes. The leading theory as to why this change worked is that in the absence of gold metal oxidation at the insoluble anode, there are still other byproduct reactions at the anode.
The reduced diffusion layer at the anode does make the desired reaction more efficient, but it also makes the byproduct reaction more efficient at an even greater rate. When the diffusion layer at the anode was increased with the new flow path, the byproduct became less efficient while the desired reaction efficiency remained intact (Figure 5). What this tells us, beyond this particular instance, is that a renewed fundamental understanding of electroplating is available to inform the semiconductor industry going forward.
Looking Forward
What this documented experimentation means for semiconductor manufacturers is that the way things have been done is not the way they should be done when new and improved tool configurations are introduced. Electroplating tools have acquired immense capability over the years through complexity demanded by a particular market, while other technologies have not received adequate attention.
What if that complexity is not needed for every corner of the semiconductor field? Can we rethink the way we design equipment to provide the capability that is needed by often-neglected chip producers without added complexity? By revisiting fundamental plating principles, we believe that the era of ‘More than Moore’ will better serve the diverse compound semiconductor and overall power electronics market.
Cody Carter
Stan Wright