400 km range with just 15 minutes charge
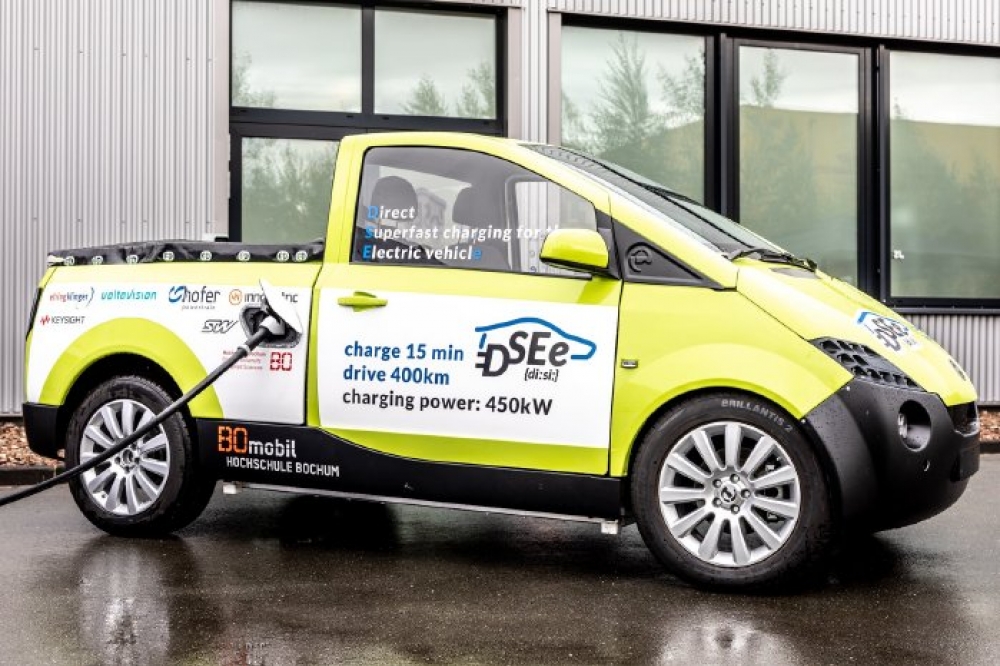
German research partners develop new charging tech and vehicle prototype to store energy required for a real 400 km range in 15 minutes
As part of the research project 'Direct Superfast charging for the Electric vehicle' (D-SEe), the participating cooperation have partners developed a new charging technology and a vehicle prototype to store the energy required for a real 400 km range in just 15 minutes.
During the four and a half years of research, funded by the German Federal Ministry of Economics and Climate Protection, the partners hofer powertrain, Bochum University of Applied Sciences, innolectric, Keysight Technologies, Sensor-Technik Wiedemann (STW), and Voltavision analysed and optimised the entire energy flow chain from the power grid to the charging electronics and the charging cable to the vehicle battery.
The result is a fast-charging station with 450 kW charging power and a prototype vehicle suitable for reproducibility, which together are able to charge the energy required to drive 400 km into the vehicle battery in just 15 minutes.
For a range of 400 km and the 88 kWh usually required for this, the charging process at charging stations with a power of 50 kW takes more than one and a half hours. Porsche's Taycan 4S is faster, charging at an average of just under 170 kW between 0 and 80 percent charge. Since a maximum of 150 kW of this power is actually stored in the battery, the Taycan would need at least 35 minutes to charge 88 kWh - if its battery were large enough.
"The challenge of the research project was to further optimize this charging power and, to this end, to modify and further develop the electronic components, charging cable technology and vehicle battery that have been common on the market to date," says Kai André Böhm, professor at Esslingen University of Applied Sciences and project manager of the D-SEe research project. Every component used had to meet the high project requirements and was thus subjected to the most exacting tests in terms of efficiency, costs, comfort, and service life. Existing norms and standards also had to be taken into account, such as the standard-compliant implementation of DIN SPEC 70121, which defines the basics of DC fast charging.
Böhm says all of the companies have been active in the field of electromobility for years and were able to contribute their in-depth expertise to the research project as a clear advantage. If the components commonly available on the market were not suitable for project implementation, the project went into in-house product development. For example, the Bochum-based company innolectric developed a new standard-compliant charging communication system, the DC Charging Controller, specifically for the fast charging process.
Keysight Technologies designed new advanced power electronics for the fast-charging process, which enables power of up to 450 kW reliably over longer periods of time due to SiC technology. As a result of this technology, the prototype vehicle from Bochum University of Applied Sciences can be powered with around 400 kW of power at 460 A and up to 900 V. This would overload a normal vehicle with a common vehicle battery by a factor of four because the power loss in the battery increases by approximately quadratically with the charging current.
The appropriate battery type was developed by hofer powertrain and the University of Bochum. The aim was for the vehicle battery to have an optimum power-to-energy ratio, thus enabling an efficient compromise between heat generation, service life, and range. The various cell formats that made it to the shortlist were tested by the high-voltage test service provider Voltavision. The standardized and automated test procedures were modified again and again during the research project and in some cases newly developed by Voltavision.
The final battery prototype now shines with cells with a P/E ratio of 3.5 and an energy density of 210 Wh/kg. The new high power prototype battery with Li-Io technology has a voltage of 645-903 V and can hold around 128 kWh. Various strategies for the actual charging process were also tested by hofer powertrain and employees of the Bochum University of Applied Sciences. The selection of the cells allows a charging process with a constant current of 460 A due to the optimal P/E for the fast charging process. It was possible to dispense with an elaborate cooling concept, as the battery temperature only rises by 26 °C during the fast charging process. The appropriate Battery Management System (BMS), which enables high voltages and maximum charging power, was implemented by the company Sensor-Technik Wiedemann (STW).
"We are pleased that we were ultimately able to exceed our targets during the four and a half years of the project," explained Kai André Böhm at the final presentation of the research project, "because with an average discharge power of 70 kW and a discharge energy of 90.3 kWh, we achieve an overall efficiency of 92 percent." In addition, all the companies involved benefit from the research and development work carried out as part of the project. The development of new test methods, high-end charging electronics, and a new communication module, in addition to a real 410 km range (WLTP: 564 km) at 88+ kWh and 15 minutes charging time, are definitely interesting project results that will influence the development of eMobility.
"This fast-charging technology will be found in passenger cars in the future," said Christoph Dörlemann, Section Manager Technology Center of Keysight Technologies, when asked to what extent implementation in series production is conceivable.