IGBT Modules Interrogated Acoustically
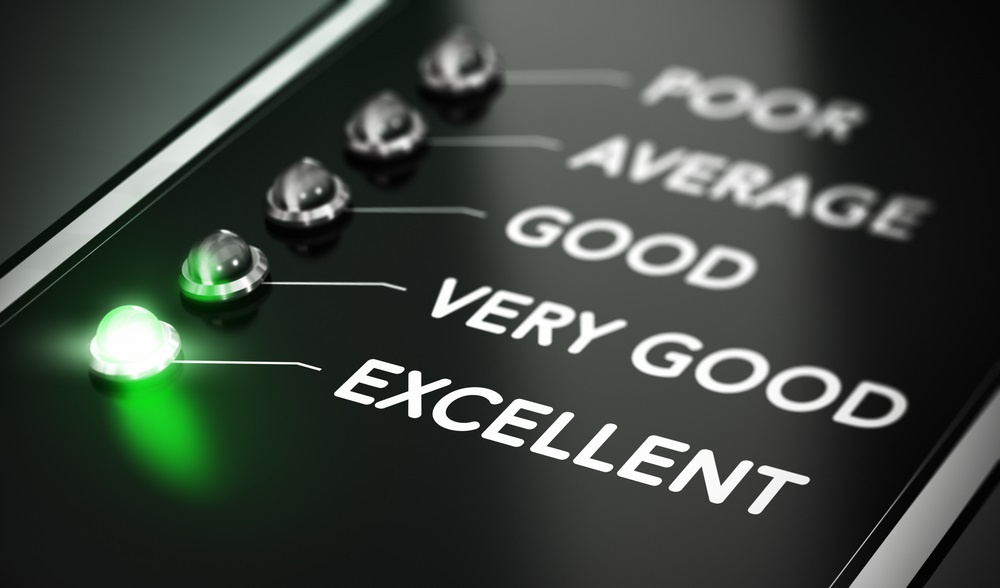
IGBT failures, because of the typically high voltage and power levels, can be both costly and dangerous. It makes sense to find internal structural defects before they have an opportunity to go wrong by Tom Adams, consultant, Nordson SONOSCAN
A group of three small air voids is trapped in the solder that bonds an IGBT module to its heat sink. The voids happen to lie close enough to each other to prevent some of the heat from escaping cleanly from the area of the die just above them. Over time, the area above the voids may overheat and the die may fail electrically - and along with it the system it is part of.
IGBT failures, because of the typically high voltage and power levels, can be both costly and dangerous. It makes sense to find internal structural defects before they have an opportunity to go wrong.
X-ray and ultrasound can both perform the nondestructive imaging that is needed, but with some differences. The first is penetration. X-ray may not adequately penetrate the heat sink on some IGBT modules, to deliver its data. The X-ray beam reports local differences in attenuation, and the most frequent defects in IGBTs are air gaps and non-bonds. If the gaps are relatively thick, such as a void in solder, imaging may succeed, but if they are very thin, as in a non-bonded area, they may remain invisible because their impact on the beam’s attenuation is too slight.
An Acoustic Micro Imaging tool such as a C-SAM® tool from Nordson SONOSCAN can readily penetrate the heat sink, but first it needs to solve another problem: the small water column that on other components couples the tool’s transducer to the top of the component cannot be used on the top surface of an unencapsulated IGBT module. Impure water coming in contact with the face of the module could invariably leave some residue from evaporation, and the IGBT’s voltage level is so high that the residue could become a conductive pathway, with disastrous consequences. IGBT modules area one the few comps types the only component type having this limitation.
For this reason an inverted acoustic micro imaging tool was developed in order to image IGBTs from below, through the heat sink. The transducer and its water column both point upward at their station below the module, whose top surface remains dry. Because the bottom side of an IGBT module not covered by encapsulant, the modules can be imaged even after encapsulation.
As the tool’s transducer scans back and forth along the bottom surface of the heat sink, it carries out its pulse-echo function at individual x-y locations tens of thousands of times per second, and contributes one pixel for the acoustic image with each pulse. The sequence is this:
• the transducer launches a pulse upward into the column of water.
• the pulse strikes the water-to-heat sink interface, and is in part reflected back to the transducer and in part transmitted upward into the module.
• the reflected echo reports, among other things, the distance from the transducer to the surface of the heat sink at the bottom of the module
• the transmitted portion travels through the heat sink and reaches the interface between the heat sink and the solder
• the heat sink-solder echo is reflected to the transducer, where it reports the distance and other data about the interface.
The process will continue upward through additional material interfaces until the pulse reaches the attachment of the die to the raft. But before it reaches the raft, it will report any unintended features it encounters in the solder. The unintended features consist almost entirely of air gaps, which may take the form of air bubbles in the solder or flat delaminations between two solid materials. This is when the three voids mentioned in the first paragraph would be imaged, and their distance from the heat sink surface recorded.
The air bubbles are actually the most imageable features in the module, because instead of presenting a solid-to-solid interface, they present a solid-to-gas (air) interface, which reflects more ultrasound (nearly 100%) back to the transducer than any other type of interface. Solid-to-solid interfaces tend to reflect 10 to 50 percent of the energy in an arriving pulse. No ultrasound penetrates the solid-to-air interface, so x-y locations lying directly beyond it will not be imaged.
Figure 1 Monochrome acoustic image made by scanning through bottom of module shows defects in one die attach.
You can see these effects at work in the monochrome acoustic image in Figure 1. To make this image, ultrasound was pulsed upward through the heat sink, the solder, the raft, and the die attach material, and returned to the transducer by the same route. The rounded white feature near the upper left is an air-filled void in the layer bonding this chip to the ceramic raft in the module. There is another large void near the lower left, and several smaller ones.
This image was made by using a ‘gate.’ Since the pulse was launched three material layers below, to make the desired image the receiver needs to select only the echoes from the small slice of time during which echoes were reflected by this die.
At each x-y location, the transducer’s receiver waits after a pulse is launched until at precisely the right nanosecond after launch it is activated to accept whatever arrives from the gated depth - anything from no echo to, as here, the strongest possible echo. Probably thousands of ‘strongest possible’ echoes arrived at the receiver to make the x-y shape of this void appear white. Weaker echoes produce gray. No echo at all yields black.
There seem to be a few cracks in this die, visible as dark lines; one reaches the void at upper left. The indistinct black features mostly on the right half of the die are voids in the solder layer, which is closer to the transducer. They are above the gate set for the die that is being imaged. They are black because they are shadows from voids above the gate.
Being voids, and filled with air, they sent back their own echoes when the pulses coming from the transducer struck them, but their own echoes arrived at the transducer too early to be within the collecting gate and were ignored. But by preventing pulses from reaching the die, they sent their own acoustic shadows to the transducer. One might also explain the same phenomenon by saying that during the brief moment when the transducer was receiving echoes from the die attach, the areas beyond these voids had nothing too contribute.
Figure 2 Light blue features are closest to heat sink, pale green are farthest above.
Figure 2 is the acoustic image of the raft surface on one of the die on a IGBT. The colors here are reporting the vertical distance of the solder-filled space between the raft and heat sink surfaces. This figure extends vertically through the whole thickness of the solder. The raft is deepest in small areas at left center (pale green in color map at left) and highest at upper right (pale blue in color map), where there is so little solder that the raft surface probably comes close to touching the heat sink.
The key features here are the n on-uniform thickness of the solder and the numerous heat-blocking voids, some of which are quite large. Collectively they may be capable of causing a region of the die just above to overheat and fail. Those voids that are light blue are likely in contact with the heat sink. But note that part of the upper right corner is the same color, because the solder in this region is very thin. The large blue C-shaped void near the center lies above another large void that lies in the red-yellow depth. Non-uniform solder layers may lead to uneven heat dissipation and therefore unwanted stress. Non-uniform solder layers may lead to uneven heat dissipation and thus unwanted stress.
Neither of the IGBT modules shown here would be candidates for incorporation into a product: they are simply too filled with anomalies. But in these high-power modules even a single small anomaly could lead to failure if the modules are being used close to their design specifications.