Improve EV Battery Pack Designs with CAD-Embedded Thermal Simulation
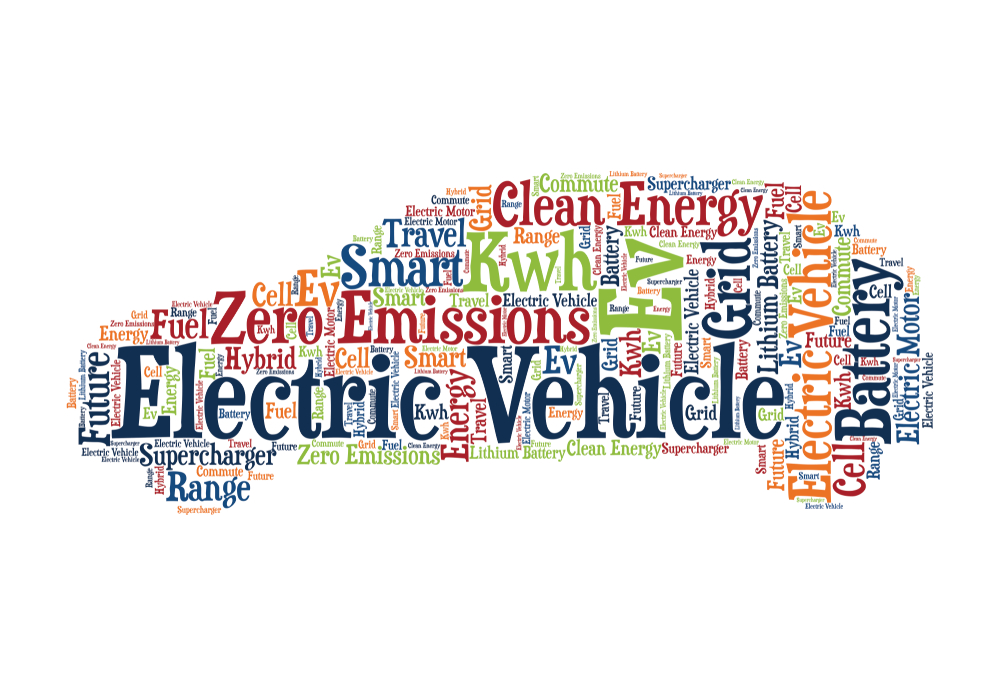
Germany, Britain, Norway, The Netherlands, and France have announced bans on new internal-combustion engines within the next 5 to 15 years; other countries are calling for gradual phase-outs of fossil fueled vehicles or increasing the share of electric vehicles (EVs) and hybrid EVs on their roads by 2050. In the United States, this movement is being led by California. China is expected to be the largest market for electrical vehicles (EVs). Predictions are that by 2040, 54% of new car sales and 33% of the global car fleet will be electric [1].
Some of the important challenges in EV development and sales are getting more than 200 miles out of a charge; pricing below (USD)$40,000; fast charging"”meaning less than 30 minutes recharging time for an 80% charge; increasing fuel efficiency over a larger range for hybrids, and the development of autonomous vehicles. Many countries and major cities are pushing for the electrification of not just cars, but also industrial, public service, and mass transportation vehicles.
For the electric powertrain, the engineering focus is on the price and size of battery packs, motor efficiency that effects driving range, and the trade-off between drive range or performance (balanced against) ever-increasing driver experience requirements and features. Energy storage needs to be designed so that it obtains the required energy and power density in each battery cell as well as the overall pack. The pack has to be thermally regulated so that it won't overheat. Energy storage has to be monitored and optimized while driving.
The motor and power electronics need to be optimal for the architecture, weighing efficiency vs. performance vs. cost. Here also, thermal management and reliability are important issues. The power electronics need to be reliable over a wide range of operating temperatures, and design is a challenge with the inverter and motor inside a single casing.
The skills of computational fluid dynamics (CFD) experts traditionally have been necessary for electric powertrain, as well as component-level design, and to expose underlying limiting phenomena. However, relying solely on CFD experts today can result in either slower deployment or under-achievement of the expected design.
A new approach, where automotive designers can use the CFD tools easily as early as possible in the design phase to evaluate prototype designs and optimization, is gaining traction among OEMs and Tier-1 suppliers. This front-loading, designer-centric approach rests on three elements: 1) CAD-embedded CFD that allows complex simulations to be done by non-CFD experts in the native CAD environment of designers; 2) simulation automation and a built-in database to allow engineers to achieve reliable and accurate results; 3) seamless integration with electronic design automation (EDA) and system simulation tools. Using this approach, we have seen results that reduce the time and cost as much as 60 percent [2].
Battery-Pack Design and Prototyping Case Study
Let's look at a real-life example of where this approach has shown immediate benefits. The Mobilis company in Brazil builds EVs for recreational use in rough road and ambient conditions [3]. The vehicles are air-cooled with 4-kW/h battery packs. The company obtains battery packs, or battery cells, from their suppliers, and then they integrate them into their vehicle designs (Figure 1).
Figure 1: Battery pack housed at the floor of a Mobilis vehicle.
The design engineers needed to figure out what kind of geometry they would need with this particular battery pack so that the vehicle could fulfill its cooling objective in harsh climatic conditions, compared to the manufacturer's nominal recommendations. Operating temperatures that are more uniform with lower maximums result in longer battery life. Evaluation of designs on battery thermal behavior with implications for pack reliability in real-world operation is ideally suited for using a CAD-embedded CFD simulation approach.
The original battery pack design (Figure 1b) consisted of one inlet and outlet for air with an outlet port on the side that had a smaller diameter than the inlet port. In their calculations, they made an assumption about the turbulent flow for the aluminum base plate (enclosure of the battery pack) based on the likely interactions between the air and uneven geometry underneath the vehicle. Air-flow distribution within the pack has a strong effect on the battery's thermal behavior.
Assessing Thermal Behavior of both Original and New Designs
Analysis of the original design as built into the first prototype showed that the air outlet location wasn't optimal for their needs; the constrained space between the cells and the air outlet port rendered insufficient air flow. The temperature reached an unacceptable 84 °C, so the engineers decided to change the geometry of the pack to increase the air flow.
After design iterations using simulation and analysis, they added another inlet and outlet, shifted the air-outlet ports to the side, and increased the outlet ports' diameter to match the inlet ports. Figure 1c shows the new CAD design, and Figure 2 shows the air flow (pressure distribution) in the redesigned pack compared to the original.
Figure 2: Air-pressure distribution inside the redesigned battery pack (left). In the original design (right), the constriction at the outlet is clearly visible.
The engineering team was able to eliminate flow constriction near the outlet and had fewer areas of flow stagnation compared to the original design. Also, the new design improved the air-flow rate in the narrow area of battery cells and battery pack enclosure, which helped convective heat transfer. Figure 3 shows the resulting temperature distribution in the new pack. The maximum temperature was 54 °C (compared to 84 °C for the original design), which was well within the cell manufacturer's maximum recommended temperature.
Figure 3: Temperature distribution in the redesigned battery pack for nominal operating conditions. Maximum temperature in the pack's new design is 54 °C.
Simulating Extreme Operating Conditions
The next step was to simulate the thermal response of the redesigned battery pack under critical conditions (Table 1), compared to "normal" conditions, which they considered to be a warm day at 30 °C, carrying a medium load, at slow speeds (25 kph or 15 mph). Critical is defined as extreme operating conditions that the vehicle may be exposed to for short periods of time, but is not designed to operate in continuously, using three times more power per cell with half the available airflow compared to normal.
Their analysis showed that the redesigned pack would reach unsafe temperatures as high as 110 °C, if the vehicle was operated under such critical conditions continuously. They wanted to be able to estimate temperature ramp up in the battery pack once it was subjected to these extreme conditions, and if it would be enough that the system needed to react.
Under such conditions, the battery pack could operate for approximately 78 minutes from rest conditions before the battery-pack temperature rose beyond the maximum recommended temperature of operation (60 °C). Figure 4 shows the temperature rise in the battery pack when subjected to these critical operating conditions. Because of the battery's large thermal mass, this slow temperature rise rate provided enough time to take necessary actions to avoid damage to the battery pack that would limit its life; this design change was deemed a success.
Figure 4: Temperature rise in the battery pack over time when subjected to critical operating conditions.
Summary
Working with a consultant at Creative Solutions, Mobilis engineers leveraged the CAD-embedded computational fluid dynamics (CFD) software, FloEFD, for optimizing their battery-pack design. Starting with an initial CAD design of the battery pack, they simulated dozens of scenarios to explore the battery thermal behavior with changes in the battery's design. Through this process, the engineers reached an optimized battery-pack design much more quickly than if they had needed to send out their models for CFD analysis using the traditional approach in which significant, specialized engineering efforts would have been dedicated to CAD-to-CFD translation.
Through these simulations, they were assured that the cooling system would be adequate for the harshest cases, such as driving on a long steep uphill with the vehicle loaded, when the asphalt is hot, or starting the vehicle when it has been parked outside on a sunny summer day. The simulations were instrumental to understanding how use-conditions could negatively affect battery life and which operating conditions should be avoided by customers, as well as for devising strategies to mitigate liability issues that can be caused by misuse or random unpredictable system failures.