SiC wafer scribing is particle-free
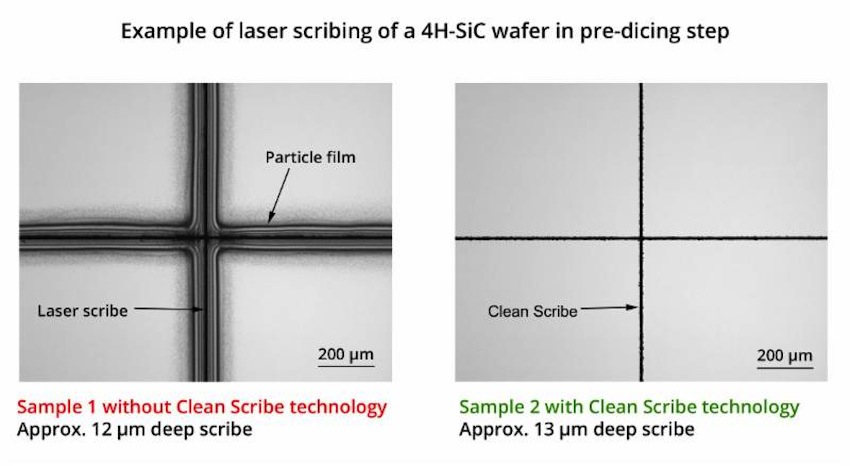
3D-Micromac's Cleans Scribe technology eliminates need for expensive wafer coatings without impacting wafer dicing throughput
3D-Micromac AG, a supplier of laser micromachining and roll-to-roll laser systems, has unveiled its Clean Scribe technology, a new patent-pending feature for its microDICE laser micromachining system that enables particle-free scribing of SiC wafers without the need for expensive coatings and without impacting wafer dicing throughput.
"Consumer demand for hybrid and electric vehicles, as well as growing use of automotive electronic systems for improved fuel efficiency and driver safety, is fueling the need for SiC-based power devices," stated Hans-Ulrich Zuehlke, product manager at 3D-Micromac.
"Maximising yield on the production of power devices is paramount to ensuring consumer safety for these applications. At the same time, driving down costs throughout the SiC power device manufacturing process is crucial to enabling wider adoption of these advanced vehicles by consumers. Our new Clean Scribe technology is the latest example of 3D-Micromac's commitment to continuous innovation of our TLS-Dicing process in order to achieve greater yield, throughput and cost savings in device pre-packaging as well as to expand the applications that can benefit from our technology."
Scribing is an essential step in wafer dicing. 3D-Micromac's TLS-Dicing approach is a two-step process involving the use of a short ablation laser to produce an initial scribe at the beginning of each cut in the dicing street in order to initiate a crack.
This 'dry' scribe process generates a very low number of particles. Then, in the second step, a continuous wave laser is passed along this line to heat up the material locally, which is then rapidly cooled by spraying with deioned (DI) water, cleaving the wafer.
To enhance the reliability and straightness of the cleave, the initial scribe can be performed across the entire length of the dicing street. However, this 'continuous scribe' can generate a greater number of particles, which may be too much for certain particularly demanding SiC applications.
To avoid this, customers previously needed to reduce the speed of the scribing process or apply an additional wafer coating step before dicing to prevent particles from falling into the dicing street. However, this step adds significantly to process complexity and cost.
3D-Micromac's new Clean Scribe technology uses a patent-pending laser scribing process that eliminates polyimide and metal particles in the dicing street, enabling a virtually particle-free surface without the need for expensive coatings.
Clean Scribe replaces the 'dry' scribe approach with an aerosol spray that uses an extremely small amount of DI water (less than 20 ml/min) to wash away the particles during the laser processing step. Since the TLS-Dicing process already uses DI water and compressed air for the cleaving step, no additional systems or consumables are needed with Clean Scribe. At the same time, Clean Scribe achieves these results with no loss of throughput - enabling wafer dicing speeds of up to 300mm/sec.