New IGBT Designs Close Performance Gap with GaN Transistors
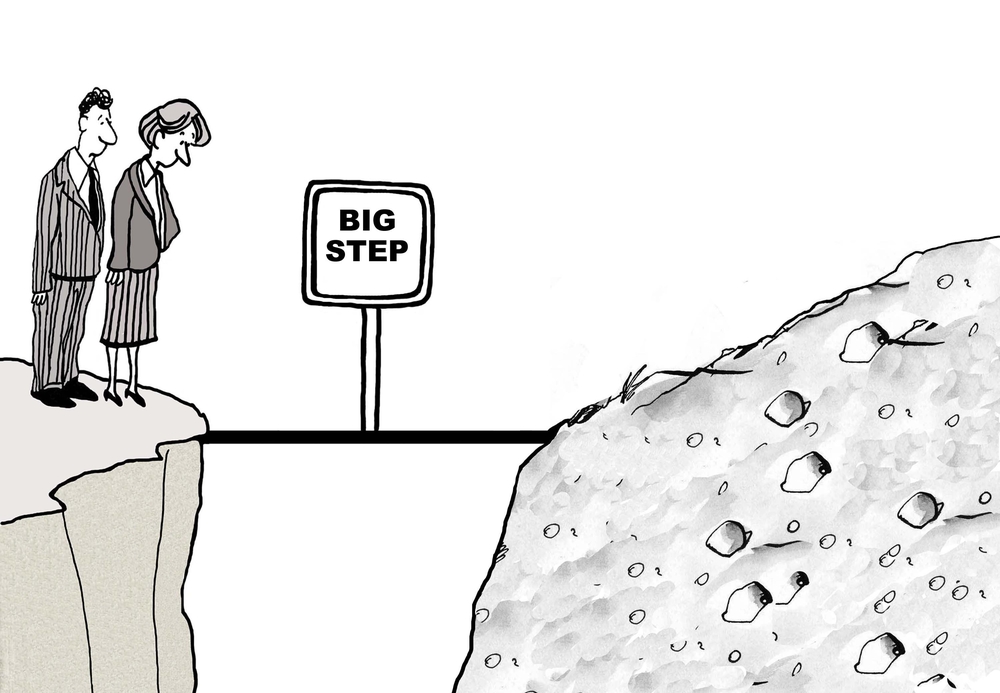
As gallium nitride (GaN) and silicon carbide (SiC) transistors move into mainstream power applications, silicon device manufacturers are advancing IGBT performance to give designers more power handling options. By Akhil Nair, Technical Marketing Manager for IGBTs, ON Semiconductor
Insulated gate bipolar transistor (IGBT) devices are vital components in high performance power conversion (HPPC) circuitry. While power MOSFETs are generally used for low/medium voltage implementations, IGBTs (which have voltage ratings in excess of 1kV) are highly optimized for deployment in challenging higher voltage environments. Improving operational efficiencies and reducing losses are now the fundamental concerns for engineers using these devices. The following article tackles this subject in detail.
While wideband gap technologies, such as gallium nitride (GaN) or silicon carbide (SiC) hold a lot of promise for the future, this is still a long way from being a cost-effective strategy for the vast majority of applications - the unit pricing would just be too high at this stage. It is estimated widespread uptake of GaN/SiC technologies probably remains at least 5-8 years away, as technology maturation and greater economies of scale are needed in order to bring price points down to an acceptable level. So, with this option not yet commercially viable, there is a pressing need for some sort of alternative.
Instead of implementing a move to new semiconductor materials, the industry has to find a way to push the performance envelope of existing IGBT technology. The question remains: How is this going to be done?
Application Demands
Advances need to be made so that high voltage IGBT devices can support the elevated frequency levels that are now being demanded, which often extend above the 20 kHz mark as a minimum for many Hi-Performance Power Conversion (HPPC) application. This sort of performance is being expected in a growing number of application areas - among them hybrid/electric vehicles (HEVs), solar infrastructure, uninterrupted power supply (UPS) units and HEV charging stations. Power efficiencies at these higher frequencies has to improve significantly in these applications (heading towards figures of 95% in many cases). This implies that switching losses in traditional IGBT technologies need to come down in order to meet these application demands.
Combating the thermal issues associated with IGBTs is also of great importance and should not be overlooked. In today's complex power system designs, space is normally quite constrained. By improving switching performance and consequently system efficiency, the area that needs to be taken up by heatsinking mechanisms can be minimized. This leads to better board space utilization and lower bill of materials costs while still ensuring the reliability is maintained.
The only way to enhance the performance characteristics of IGBTs, while staying with Si technology, is to explore new approaches in relation to how these IGBTs are designed. There are 2 important criteria that define IGBT operation and impact most acutely on its power efficiency. Firstly, there is the total switching loss (Ets), which is the sum of the turn-on (Eon) and turn-off (Eoff) switching losses. IGBT switching losses can be substantial, especially when the device is running at higher switching frequencies and/or elevated operational temperatures. Secondly, there is the conduction loss to factor in, which relates to the collector-emitter saturation voltage (VCEsat). An unavoidable trade-off exists between the switching loss performance and conduction loss performance. It does not achieve anything, therefore, to simply concentrate on reducing switching losses. Design engineers need to look at the whole device, rather than a single element in isolation. It is commonplace to refer to the following figure of merit (FoM):
FoM = VCEsat x Ets
This FoM gives engineers a consistent way by which to benchmark the performance of IGBTs and compare the devices offered by different vendors.
Addressing IGBT Switching Losses
As mentioned earlier, with IGBT switching performance fundamentally consists of two components: Eon and Eoff.
The Eoff of an IGBT can be reduced by two means;
A) by increasing the speed of the device i.e. decreasing the high to low transition time
B) by cutting the tail current
Thermal management concerns should be a part of application demands
Figure 1 shows the two different scenarios where Eoff is reduced by the methods mentioned above. As seen on the grey waveforms, reducing Eoff by increasing the speed (very high di/dt) of the device results in significant ringing. Not only is this undesirable from an EMI standpoint, but the oscillations also contribute to increasing losses; there is the added risk of device destruction if the peak voltage exceeds the device breakdown voltage. The alternate approach (green waveforms) of reducing the tail current is clearly more preferable since it allows for reduced losses while maintaining a soft and smooth turn-off profile.
Figures 1: Two approaches to reducing Eoff
While Eoff is almost always considered a key measure of IGBT technology, Eon is oft ignored as it is dominated by the co-packaged rectifier. While this is true, when considering the device as a whole and its impact on system performance, it is important to not ignore the Eon since it can significantly contribute to system losses. As seen in Figure 2, the diode reverse recovery performance is improved by reducing peak reverse recovery current (IRRM) and reverse recovery time (TRR). It is important to realize that too low a value for TRR would give very high dIRRM/dT, resulting in ringing. Therefore the best approach to reducing reverse recovery losses (and by extension Eon of the device) is by reducing IRRM.
IGBT manufacturing challenges
Virtually all IGBTs today are designed as "˜vertical' devices (i.e. the emitter and gate terminals are patterned on one side of the wafer substrate while the collector terminal is on the other side.) The FoM of the device is inversely proportional to the thickness of the wafer that the device is constructed on (i.e. the thinner the wafer the higher the FoM of the IGBT.) IGBTs today are routinely constructed on wafers <200µm.
Essentially the most straight forward way to improve the FoM of an IGBT is by reducing its thickness. However using thinner wafers has some significant challenges. Obviously, handling wafers that are as thin as a human hair present major issues during manufacturing. But, more importantly, reducing the thickness also results in a lower breakdown voltage. Most recent IGBT technologies employ field stop technology to reduce the thickness while maintaining the breakdown voltage. This technology introduces a buffer layer (called a "˜field stop') between the collector layer and the bulk of the silicon. The field stop layer, in addition to allowing a higher breakdown voltage also has the added benefit of reducing the Eoff of the IGBT. While a thick field stop layer is very desirable from a device performance standpoint, the silicon processing techniques required to create one are not simple.
Next-Generation IGBT solutions
Utilizing the company's proprietary Ultra Field Stop (UFS) trench technology, ON Semiconductor has now introduced a series of 1200V IGBTs with a very high FoM. The standard 1200 V/ 40 A device made with UFS technology has ~40%lower ETS and 15% lower VCEsat than the best most devices available in the market today. This means that these devices can offer the high degrees of performance now being stipulated, curbing system energy losses and boosting power efficiency levels.
The UFS devices are built on SOI (Silicon on Insulator) substrates. UFS is also the first time that wafers which are only 105µm thick have been used by 1200 V IGBTs. The ultra-thin devices are of course enabled by an extra thick field stop layer. The combination of the thick field stop layer and thin wafers contributes to these devices having such a superior FoM.
Another contributor to the performance improvements delivered by these device is the highly advanced platinum-silicon based rectifier that is co-packaged with the IGBT element. This is optimized specifically for operation in conjunction with the UFS technology. It assists in enforcing the desired reduction in reverse recovery losses without ringing.
Figure 3 shows the difference in power losses on a standard half bridge inverter, when comparing the UFS device against On Semiconductor's previous generation of industry standard FS2 technology. The details of the application conditions under which the measurement was performed is shown in the figure. The results illustrate how significant reductions in the power losses are experienced With UFS technology.
With the widespread adoption of GaN on SiC some time away, power IC vendors need to provide the markets they serve with high voltage switching devices that are still based on established silicon processes; IGBT technology is certainly one that currently holds a lot of promise. The combination of newer IGBT technologies such as UFS, combined with advanced fast recovery diode technology has enabled power efficiency levels to be pushed further higher to satisfy application demands.